Digitalisation of ore composition and its benefits
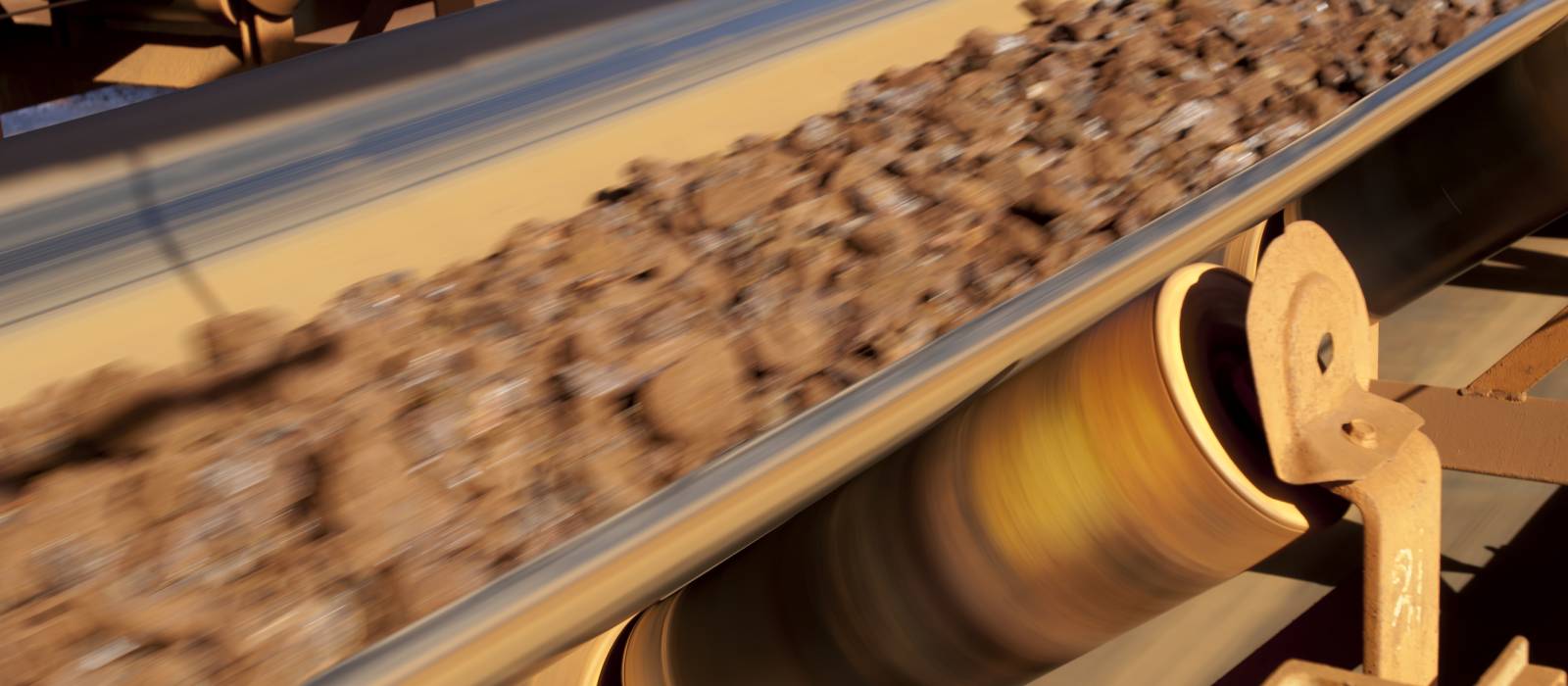
An examination of sensor technology and how good quality measurement data provides the foundation for digitalisation success.
The problem
Mined ore quality varies due to natural differences in mineral concentrations, irregular ore boundaries, and mining processes. Grade control systems attempt to segregate ore and waste so ore is sent to the process plant and waste is discarded. Variation is almost always present within the material sent to the process plant (Figure 1).
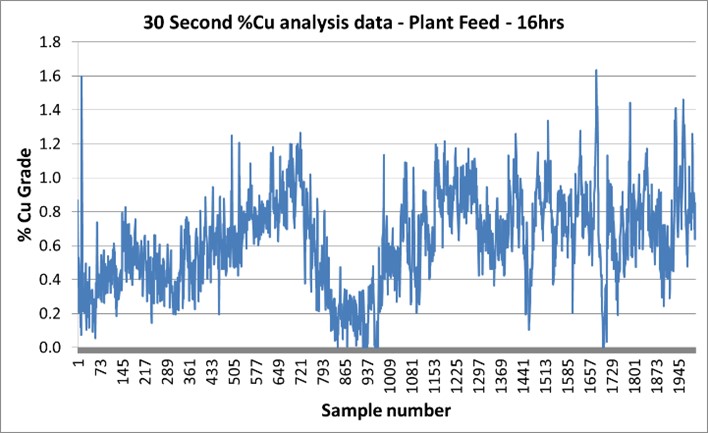
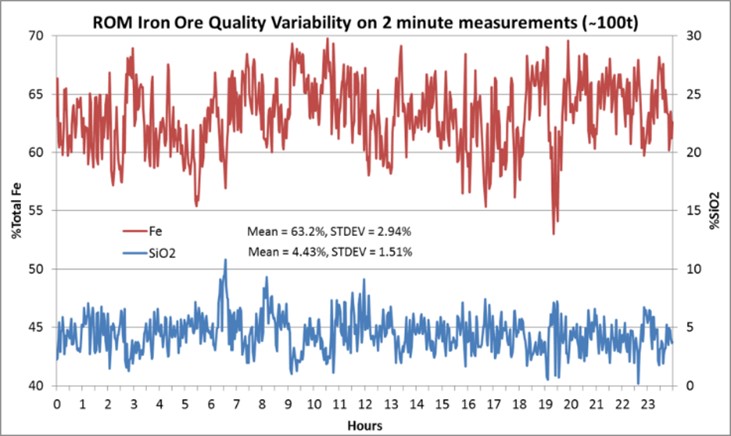
Metallurgists extract the greatest value possible from the ore they receive. Goodall (2021) discusses the large impact ore variability can have on process performance in reducing metal recoveries by up to ten percent as well as inefficiencies in power, water and reagent use. Figure 2 shows one example of the impact of head grade variability on copper recovery.
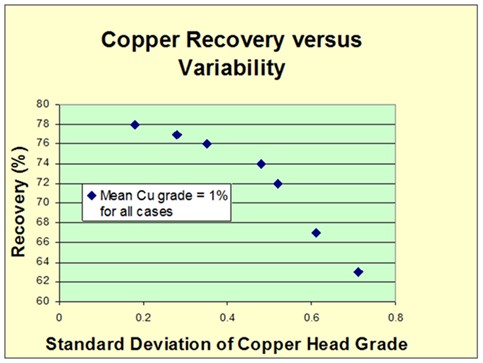
Composition parameters that affect process performance include metal grade, deleterious minerals, ore hardness, ore mineralogy, clays, carbonaceous content, acid consuming gangue, moisture, ore textures, and more. Mining key performance indicators tend to focus on quantity rather than quality, hence ore + waste = more ore, when really ore + waste = less value, wasted opportunities and lower revenues. So how do we turn this around using digitalisation?
The opportunities
Digitalisation converts an ore flow into digital data (real time ore quality and quantity). It is well accepted that measurement is required in order to quantify, control and improve processing. Technologies are available that can measure some useful composition parameters to quantify the variability, and selecting the most appropriate via a due diligence process should consider the following [non-exhaustive list]:
- technology suitable for parameters to measure, or proxies
- is measurement representative or partial, eg penetrative or surface
- data frequency (time or tonnage increments) fit for purpose
- implications of measurement performance on outcomes, sensitivity to precisions
- type/format of data, accessibility and ownership
- technology and data integration with operations
- interruption to production, maintenance requirements, availability
- OPEX and CAPEX.
Quality of incoming ore, if measured at suitable precisions and frequency for appropriate parameters, can be used concurrently for real time:
- ore tracking, visibility across operation
- feedback: ore reconciliation, production reporting
- ore blending
- bulk diversion: waste or deleterious increment removal, stockpiling, bypass process, etc
- feed forward to processing: feed rate, reagents, operational geometallurgy
- metal accounting.
Objective measurement of ore and waste quality should also improve grade control where ore and waste differentiation is difficult to perform manually.
The solution
Relatively fast sensing allows decisions to be made in real time, and representative measurement provides high confidence in the data. Sensors, such as Scantech’s GEOSCAN-M that utilises high specification Prompt Gamma Neutron Activation Analysis (PGNAA), measure multi-elemental content in conveyed flows continuously and with full penetration. This type of technology has been used in the minerals sector since 2003. Quality can be measured on conveyors within the mine and between mine and mill. PGNAA is described in more detail in Kurth (2019) and a forthcoming paper by Doorgapershad and de Paor.
Representative measurement using high specification PGNAA allows higher measurement precisions to be achieved than any other techniques, such as X-Ray Fluorescence (XRF), particularly when compared over short measurement times (Scott et al, 2020). Surface measurement technologies (XRF, Laser Induced Breakdown Spectroscopy (LIBS) for elements, and hyperspectral sensing for minerals) are qualitative rather than quantitative due to material segregation in the flow, fines coating larger particles, grade by size variability, and the very small proportion of the flow exposed to the sensor. Magnetic resonance is fast and penetrative but measures only one mineral per installation, typically the main ore mineral, so does not directly measure elements or grade. Due diligence is essential due to significant measurement performance differences, even between neutron activation systems in the market.
Sensors are used to automate grade control to aid ore and waste separation, and more importantly optimise metal recovery to process feed. Sensing and diversion applied earlier in the mining process may not be optimal if a sensor with poor precision results in significant misallocation. This may occur through ore losses and dilution of ore compared to a sensor with higher precision and improved selectivity in a downstream location.
The evidence
Grade variability is present in all commodities where sensors have been used: copper, lead-zinc, nickel, iron ore, phosphate rock, platinum-palladium, gold, manganese, chromium, limestone, coal, and diamonds. This includes porphyry and other copper-gold deposits where ores have proven less homogeneous at measurement increment scales than sites expected (refer Figure 1).
The advantage of conveyed flows is the consistent presentation of material to sensors, and the high specification PGNAA sensor’s ability to measure through the full conveyed cross section continuously at very high spectral accumulation rates irrespective of particle size, belt speed, segregation (occurring in all materials handling), mineralogy, moisture or dust. Composition remains constant, unlike fragmentation and moisture which do change through materials handling (eg increasing fines proportion by up to 15 per cent through each stockpiling and reclaiming stage).
Bulk ore sorting
GEOSCAN-M has been repeatedly selected from a range of sensors evaluated in many bulk ore/waste diversion applications in copper, nickel, iron ore, coal, and platinum operations. Figure 3 shows a MMD bulk ore sorting plant configuration used very successfully at multiple sites by AngloAmerican, allowing for ore grade increases of 20 per cent to be achieved against expected upgrades of five per cent. Extensive evaluation of a GEOSCAN-M confirmed 0.02 - 0.03 per cent Cu measurement precisions, expected over the calibrated range of 0 – 2 per cent Cu, were achieved.
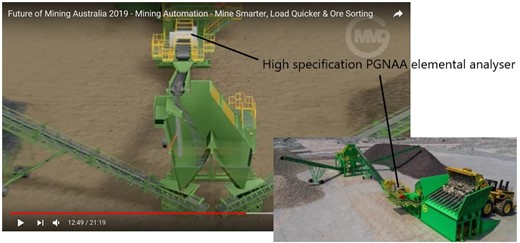
Bulk ore sorting can be combined with other pre-concentration technologies where an intermediate grade or lower grade stream can be upgraded through a particle based sorting process.
Conveyed flow measurement and diversion provides multiple benefits over upstream bulk sorting due to:
- representative measurement, providing confidence in results
- very high precisions, ensuring confidence in decisions
- much smaller increment size, optimising selectivity.
In Figure 4, the graphs compare modelled results of less precise measurement (eg lower specification or unrepresentative technology) on larger increments to more precise measurements on smaller increments. In reality the difference in measurement precisions has proven to be much greater. Table 1 summarises the results when increments are diverted in these two cases. The calculations are based on a copper metal price of USD$10,000 per tonne.
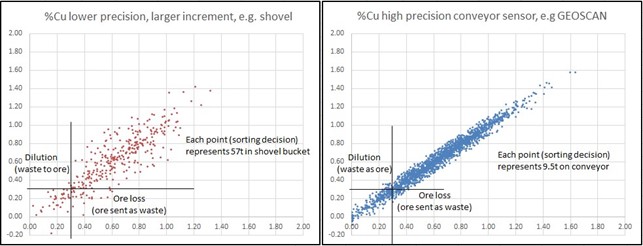
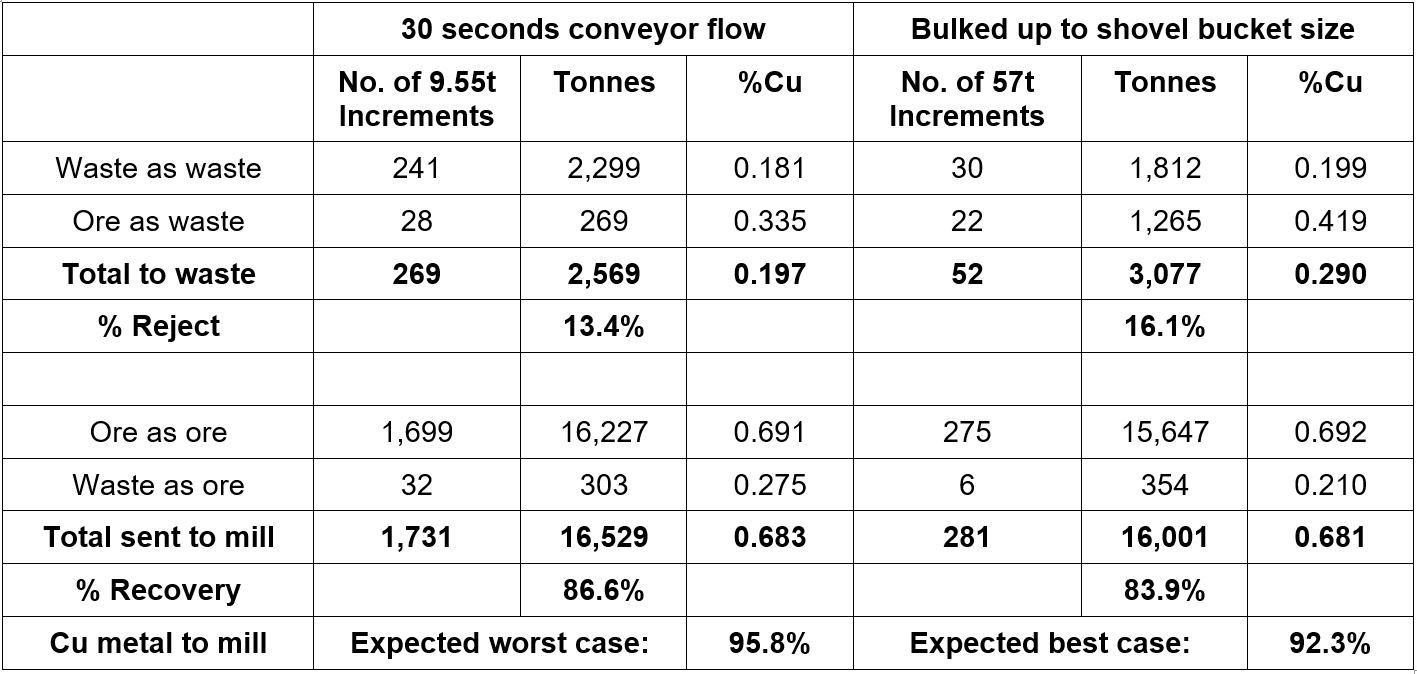
Comparing conveyed sensing using a less precise sensor over smaller increments (eg faster analysis using XRF or LIBS over 10 seconds) with a representative and precise sensor over longer increments (GEOSCAN-M over 30 seconds) indicates the more precise sensor recovers approximately USD 15 million per year more copper metal to the ore stream despite the faster, less precise sensor being considered more selective. Sensitivity of results to measurement precision is important when comparing different sensing capabilities and applications/solutions.
Measurement speed is not the primary benefit where selectivity is important, and must be balanced with precision, which is far more critical for metal recovery. Precision cannot be achieved through measurement that is not representative and measurement will not be representative if not all the material in an increment has an equal probability of being sensed.
Other applications
Measurement data should be customised to provide precision over useful timeframes for each application. Real time measurement enables control over ore blending to manage plant feed variability, which improves metal recoveries through more stable plant operations. The Sepon copper-gold operation implemented an analyser to control ore feed and additives blending, and used acid consuming gangue content to control acid addition for leach circuit optimisation (Balzan et al, 2016).
High precision measurement of plant feed provides real time feedback to mining operations and high quality reconciliation and metal accounting such as the 0.4 per cent metal accounting error achieved at Sepon copper-gold operation (J Vagenas, personal communication) and ore reconciliation to underground mining at Telfer (Doorgapershad and de Paor, in prep.). High quality measurement data enables real time evaluation of feed quality changes that affect process performance in digital twin modelling.
Average ore grades are falling in the mining industry and consequently optimising metal recovery through automated grade control and pre-concentration improves mineral resource utilisation, process plant efficiency, conservation of process consumables, reduced production of fine tailings, and improved overall sustainability of operations.
Further innovations
Sensor technologies continue to improve and further developments have resulted in analysers capable of representative measurement of phosphorus to 0.01 per cent P in iron ore, carbon content in sinter, metal contaminant measurement in scrap, black mass composition measurement in e-waste, measurement on FRAS rated conveyors and of materials such as potash containing high chlorine content, and direct measurement of trace elements such as gold, silver, mercury and cadmium. Improved capabilities continue to be developed in collaboration with customers and research organisations. Good quality measurement data provides the foundation for digitalisation success.
References
Balzan, A., Jolly, T., Harris, A., & Bauk, Z. (2016). Greater use of Geoscan on-belt analysis for process control at Sepon copper operation. Proceedings XXVIII International Mineral Processing Congress, Canadian Institute of Mining, Metallurgy and Petroleum, Quebec.
Doorgapershad, A., and de Paor, A. (in prep). The use of technology to validate metal accounting assumptions in a multisource mining operation at Telfer. Proceedings International Mining Geology 2022, The Australasian Institute of Mining and Metallurgy, Melbourne.
Goodall, W. (2021). Understanding what is feeding your process: how ore variability costs money. Process Mineralogy Today, March 10, 2021. https://minassist.com.au/understanding-what-is-feeding-your-process-how-ore-variability-costs-money/
Kurth, H. (2019). Using real time elemental analysis of conveyed ore flows to improve copper processing. Proceedings Copper International Conference, 10th Edition, 18-21 August 2019, Vancouver BC Canada, Canadian Institute of Mining, Metallurgy and Petroleum, Montreal.
Scott, M., Rutter, J., du Plessis, J., & Alexander, D. (2020). Operational deployment of sensor technologies for bulk ore sorting at Mogalakwena PGE Mine. Proceedings Preconcentration 2020, The Australasian Institute of Mining and Metallurgy, Melbourne.