Extractive metallurgy – is it an art or science?
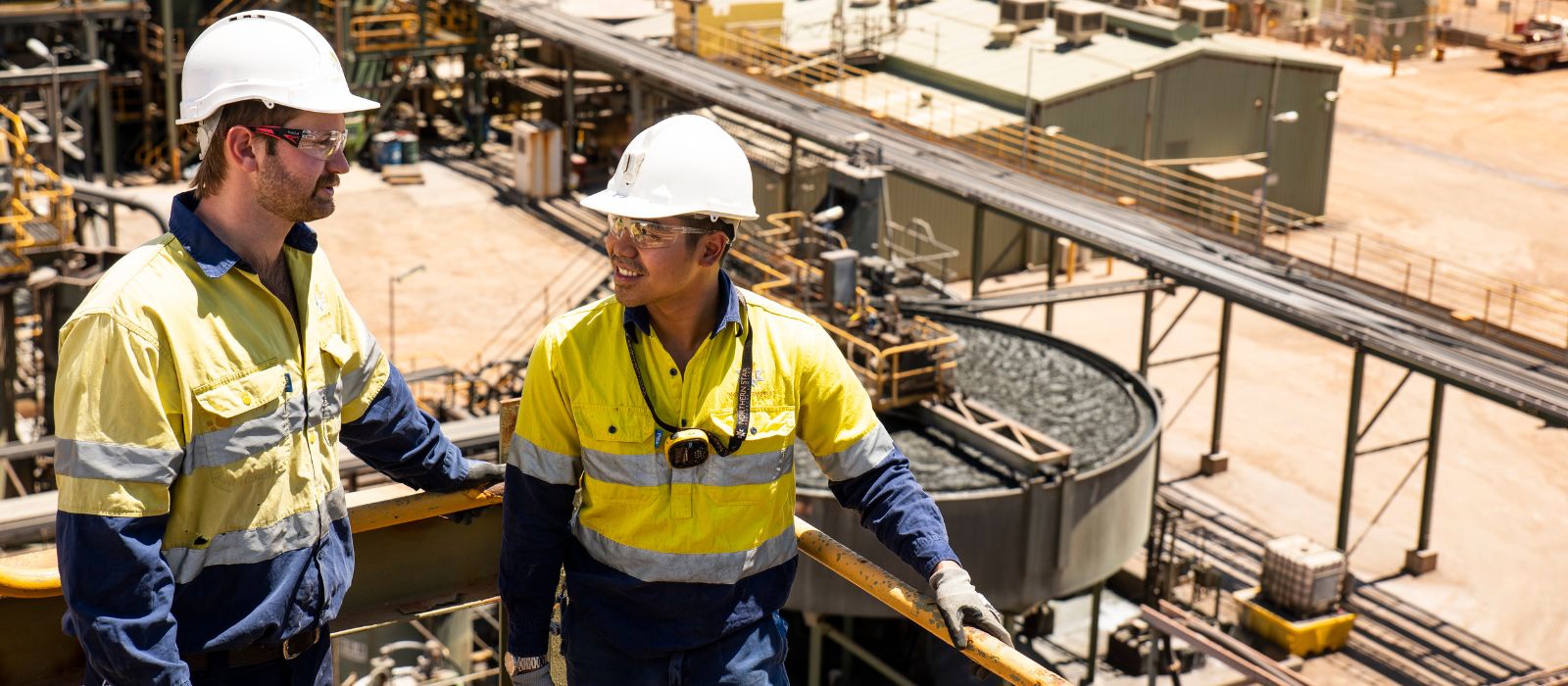
This article is based on a technical talk given by the author at the AusIMM Perth Branch in October 2022.
The obvious question to ask is, does it matter? Art and science are two of humanity’s most outstanding achievements.
Artists strive to evoke a sense of beauty or an emotional reaction through their work — whether it is in dance, music, painting, or other art forms. Art is subjective and deeply influenced by feelings and opinions.
Science is designed to be objective and guided by data. The scientific method is to observe, question, research, hypothesise, test ideas with experiments, analyse data and then draw and report conclusions.
Traditionally, art and science have been treated as two separate disciplines, but when they are studied together it's clear to see the impact one has on the other.
The great artists and scientists throughout history share the common trait of curiosity. Scientists and artists look at the world with a ‘thirst for knowledge’ and strive to understand how it works.
Metallurgy is the domain of materials science and engineering that studies the physical and chemical behaviour of ores, minerals, and their extraction. It follows this scientific method with test work and process optimisation.
Metals are crucial to our society and we’re growing more dependent on them each day. For these valuable metals to be useful, though, they first need to be extracted and purified from naturally occurring compounds in the earth’s crust and existing recycled materials. This is the role of metallurgical engineers, to design, develop and operate the industrial processes that transform these source materials into the useful materials and manufactured products essential for the functioning of modern society.
What does a metallurgist do?
Industrial scale metallurgical operations carefully combine physical and chemical separation processes to efficiently extract, refine, and recycle metals such as copper, lead, zinc, nickel, lithium and iron among others.
Metallurgy is a cross-disciplinary field with close links to chemistry, physics, engineering, and biotechnology. It operates in an engineering environment, assisting to design, commission and operate metallurgical plants. It involves the management of operations and people. The three principal fields or areas of expertise are: mineral processing, pyrometallurgy and hydrometallurgy.
The metallurgist starts with test plans, test work and interpretation and then input into the process design. This will usually involve creating ingenious and often complex flowsheets for new or revised processes. The metallurgist must never lose sight of the practical limitations involved in a process design. They develop flowsheets, process design criteria, operating costs, capital costs, equipment lists, process control philosophies and the way forward.
The practical metallurgist understands the physical problems involved in the final operation and maintenance of the designed equipment. For instance, in developing the plant layout, key control valves should be placed where they are easily accessible to the operators. Sufficient space must be available for maintenance personnel to check, take apart and repair equipment, etc. The potential health hazard to an individual by a material used in any chemical or biochemical process is a function of the inherent toxicity of the material and the frequency and duration of the exposure.
Metallurgists provide input into Environmental Impact Statements and Assessments such as examining existing data to determine the environmental safety of the project and preparation of effluent and emission summary with possible alternatives to meet acceptable standards.
The extent of instrumentation can be a factor in choosing the type of process and setting the labour requirements. Resultant savings in labour due to automatic control combined with improved ease and efficiency of operations offset the added expense of installing the instrumentation.
Innovation and creativity
Metallurgists are key innovators, the creation of new technologies and processes or the adaptability and improvement of practices is a central requirement within the mineral processing industry. An invention that is new may require legal protection via a patent. Innovations are essential throughout the project life cycle from concept, proof of concept and testing, right through to implementation of that idea in a process plant. The location of plants outside in the open was initiated by Australian engineers; prior to this, plants (including mills and flotation) were located inside buildings. The development of a compact footprint and efficient plant layout was also achieved.
The concept of contract mining, contract plant maintenance and assay laboratories were developed within the gold industry. Other developments included improved floor drainage, mill centre line layout with flat floors for access and maintenance, and the inclusion of Distributed Control Systems (DCS). Some concepts were new, and others were borrowed from different industries. An extraordinary openness and spirit of cooperation spread new ideas very quickly to develop a uniquely ‘Australian’ designed ‘outdoors’ process plants. The large number of plants being built greatly assisted this development.
Metallurgy has produced outstanding innovation over the years. Flotation was developed in Broken Hill, and it revolutionised mineral processing. It uses the separation of minerals depends on selective attachment to air bubbles, with the froth containing mineral concentrate is collected in launders.
One of the 20th Century’s great achievements was Flash Smelting, which is a method that accounts for over 50 per cent of copper smelting. It involves blowing oxygen-rich air, dried Cu-Fe-S concentrate, silica flux, and recycle materials into a 1250°C hearth furnace. Once sprayed into the chamber in the furnace, the sulphide mineral particles react rapidly with the oxygen gas. The products are:
- a molten copper-iron-sulphide matte with approximately 65 per cent copper concentration
- molten iron-silicate slag containing 1-2 per cent copper, and
- hot dust-laden off-gas containing 30-70 per cent SO2.
Another significant process innovation was in regard to Autoclave Pressure Leaching with high temperature and pressure using carbon steel for the shell/lead, with the inside being lined with refractory bricks or titanium.
Other recent advances in metallurgy are a decrease in average mineral grades leading to the application of ore sorting; complex mineralogy addressed with QEMSCAN and SEM method vs the old optical; larger equipment increasing the scale of processing; managing the scarcity of aquifer water and government restrictions for its use in production processes; and a need to reduce the costs of electricity supply. As a result, it then becomes necessary to generate novel extractive metallurgical processes that must focus on renewables.
Other developments include increasing the recovery of metals from conventional processes; diversifying the extraction of other elements and obtaining byproducts; reusing industrial waste and establishing procedures for its remediation; reducing energy use and carbon footprint.
Pitfalls and challenges
Unfortunately, it’s not all positive. Recently the art of “Gilding the Lily” in science has become a problem, where the positive words in titles, abstracts and research papers such as ‘amazing’, ‘outstanding results’, ‘groundbreaking spectacular results’. This is a deviation from the scientific method, where we should be objective.
Misinformation in science is another problem. We now find technical papers published that provide conflicting conclusions, which is confusing. In the real-world, metallurgy accounts for 15 per cent of projects failing (McCarthy, 2002) and further analysis describes the reasons behind these numbers – no piloting, new technology, unrepresentative samples, etc.
So – why become a metallurgist?
Metallurgy is a great career choice because it is interesting, challenging and a rewarding field in terms of personal satisfaction. It is wondrously complicated given the breadth of the periodic table and its importance to humankind and our standard of living. Despite this, there is now a crisis in metallurgical education, with a generation of older metallurgists retiring and the numbers of new graduates coming through is significantly lower than in the past. A number of metallurgy degree courses have shrunk with courses being closed. For our industry to survive long into the future, we need to promote metallurgy to the younger generations. One of the challenges potential students have is knowing how to find opportunities and learn about our industry. The teachers and academics on the ‘front line’ are the best places to assist in connecting industry with students.
Another question often asked is ‘What makes a good metallurgist?’ My answer to that is it is not IQ (intelligence quotient) but EQ (emotional intelligence). A good metallurgist is one, for example, with the following key attributes: the right attitude; being motivated; having clear goals; good time management; problem solving ability; and good communication skills.
While scientific understanding can help battle things like disease, hunger, and poverty when applied properly, it does not do so completely and automatically; it cannot solve all our problems. But given the unconventional nature and scale of the problems we face today, there is real value to be gained from collaborations that bridge the best talents we have in both the quantitative and qualitative domains.
In the context of the JORC Code, AusIMM and ASIC describe a ‘Competent Person’ as one that must have a minimum of five years’ experience working with the style of mineralisation or type of deposit under consideration and relevant to the activity which that person is undertaking. However, a metallurgist of five years’ experience is unlikely to have the depth of experience required to benchmark and interpret test work results at the required level without review by a more senior engineer.
The importance of leadership
It is also clear that management is both an art and a science. The above-mentioned points clearly reveal that management combines features of both sciences as well as art. Management may be considered a science because it has an organised body of knowledge that contains certain universal truths. It may also be called an art because managing requires certain skills which are personal possessions of managers. Science provides knowledge and art deals with the application of knowledge and skills.
To be successful in their profession, a manager must acquire the knowledge of science as well as the art of applying it. Therefore, management is a judicious blend of science as well as art, because it proves the principles and the way these principles are applied is a matter of art. Science teaches one to ’know’; art teaches one to ’do’. A manager who knows the principles must also apply them in solving various managerial problems. That is why science and art are not mutually exclusive, but they are complementary to each other (like tea and biscuit, bread and butter, etc.). The old saying that ‘managers are born’ has been rejected in favor of ‘managers are made’. It has been aptly remarked that management is the oldest of art and the youngest of science.
Concluding thoughts
In summary, clearly metallurgy is both an art and a science. The science on its own is not enough. We must deal with the real-world production plants. The older I get, the more shades of grey I see. 'Don't define your world in black and white, because there is so much hiding among the greys.' The science of metallurgy has made huge advances over the last 30 years. It’s a specialist area of expertise. I now understand that science cannot solve all the world’s problems.
As someone once said before: ‘We are metallurgists, not magicians!’ (McLean, 2011). Interpretation of data requires a person ‘skilled in the art’, a so-called competent person. Art and science have more in common than we would like to admit. Emotional Intelligence, EQ, is more important than IQ.
Science can learn from the arts and the arts can learn from science. Good management, good project management and leadership are arts, but they contribute significantly to the science of good metallurgy. Is metallurgy an art or science, and does it matter? Yes, it does matter – because it governs the way we operate.
References
McCarthy P, 2002. ‘Managing Technical Risk for Mine Feasibility Studies,’ Mining Risk Management Conference. Available from: https://www.ausimm.com/publications/conference-proceedings/mining-risk-management/managing-technical-risk-for-mine-feasibility-studies/
McLean E, 2011. ‘We're Metallurgists, not Magicians!’, MetPlant 2011 Conference. Available from: https://www.ausimm.com/publications/conference-proceedings/metplant-2011/were-metallurgists-not-magicians/