How mining leaders can take charge to improve safety, productivity and reduce stress
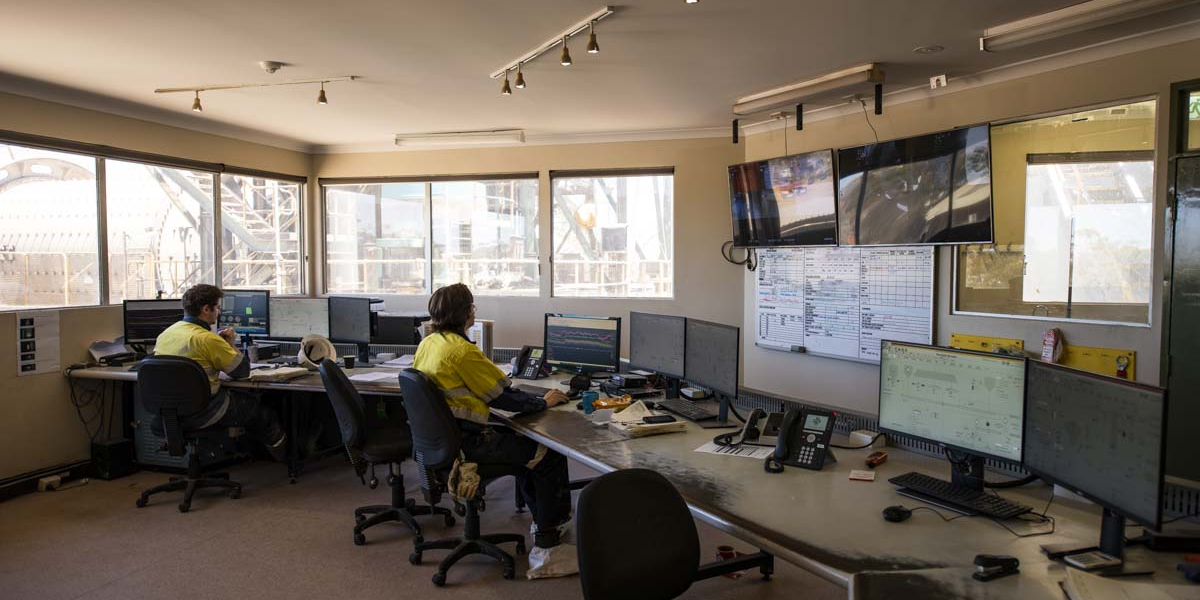
This article explores how combining a management operating system with frontline work management software can help stabilise operations, improve safety, lift productivity and reduce stress.
Mine operations are stressful. Do the below descriptions of different roles seem familiar?
Mine managers can sometimes find themselves frustrated by shift managers being unable to deliver production results according to the plan. They may also be worried about the impact the unstable production environment will have on safety.
Executives often wonder if a different General or Mine Manager would reduce the number of unpleasant surprises that the executive team are ultimately responsible for. They may also find inter-departmental trust and coordination are not what it should be, and wonder if new blood would improve things.
Shift managers are often stressed by the impediments to getting work done and meeting their targets, while making sure that everyone stays safe.
Supervisors can be frustrated with the volume of work created by head office initiatives, missing information, and difficulty in coordinating with other departments to deliver on their mandated targets. They can become upset at the blaming of individuals for poor results that are out of their control.
What causes this situation?
Production variation causes stress.
The nature of mining is such that production variation is inherently higher than in other industries, for example manufacturing. But in our experience, the actual variation is substantially higher in most mines compared to what is possible.
This wastes resources (workers become involved in non-value adding activity to satisfy a growing number of KPIs, organisational controls and data needed for ever more detailed reporting) and capacity, with the result that output can be 20 per cent or more below capability. This leads to reactive operations, with the focus on what happened yesterday and how to mitigate the mismatch between planned and actual situations, rather than looking ahead proactively.
Related content:
Not only do mining personnel need to cope with variability, but all organisations suffer from the inevitable mismatch between the actual work on the frontline and work as intended or planned by senior management. Furthermore, it is often not clear where the bottleneck is and who is responsible.
In such a pressurised environment, it is difficult to know in real-time what the actual performance is, which intermediate and long-term goals need to be pursued, and how best to coordinate activities. Coordination and cooperation suffer, and the temptation for concealing information and blame-shifting increases. In this manner, organisations can lose trust and unity of purpose, characteristics defined by Tendon and Mueller (2015) as inherent to top-performing organisations (see breakout).
In mining we see this play out through poor employee engagement scores despite significant organisational initiatives and funding. The engagement scores of frontline leaders in mining are particularly low. Frontline leaders are not only required to meet mandated production targets, but need to support head office initiatives, ensure that safety improves and hold team members accountable for results.
To compound the pressure, managers know that an unstable production environment is not conducive to safety.
What is unity of purpose?
- everybody knows the short- and long-term priorities for the overall system, their particular department, other departments and themselves
- employees are capable of making good decisions (for system performance) instantaneously.
- excellent communication
- effective coordination
- workers and managers focus on what will happen in the future, not what happened yesterday.
What is a community of trust?
- managers are comfortable delegating authority to workers
- workers know managers will support them when they act in the interest of increasing production flow
- interdepartmental trust exists, and departments know they can rely on others for support
- managers are willing to experiment and take joint responsibility for actions
- workers and managers hold each other accountable.
Organisational obstacles to taming variation
So how can people best deal with variation – and therefore stress – in mining operations?
Management practice and dealing with silos
Management practice – and the expert software tools that support management – have evolved to focus on the efficiency of individual components, often at the expense of the effectiveness of the overall system.
The fundamental belief is that humans can be managed as if they are cogs in a machine. Through business schools and large consulting firms, this way of thinking has become deeply ingrained in our mining practices, planning, accounting and budgeting systems, planning behaviours and performance measurement. Consequently, mine management is overloaded with information and local KPIs that can interfere with delivering overall desired outcomes.
The information that is critical to ensure cross-functional and cross-departmental performance is usually not immediately available or visible, and opportunities for effective collaboration across departments and functions are rare.
This can create an environment of low engagement, low productivity, and cost per unit higher than necessary. It is a straitjacket from which employees and managers can only escape with difficulty.
Planning paradigms
Mine planning is the heartbeat of mining operations. Operations will try to meet the schedule as set out and will not attempt to exceed the planned rate. Planning, therefore, sets the maximum production rate for operations. Planners do not work in isolation; they work from budgeted numbers and with information and guidance provided by operations. Any discrepancies in this information will affect the feasibility of the plan.
Many advanced mine scheduling systems are used with settings to automatically identify and work with constraints. With this setting active, the scheduler will slow down the plan to keep pace with the slowest production step. But the slowest step is usually within the control of operations and can be addressed by anyone skilled in the application of systems thinking, or the Theory of Constraints (TOC).
What a good solution looks like
A good solution to the issues explored above should free up time, make crucial data visible and enable commitment to frontline work. It should allow an operation to reliably meet and at times even exceed mandated targets. It should also improve safety performance, provide purpose, mastery and autonomy opportunities for employees and significantly increase employee engagement.
The how
The primary lever to getting control of production variability is through ‘how’ an operation is managed – not the implementation of new technology. New technology will help but is not sufficient. By adjusting the way we connect the intentions of management and planners to the work at the face, trust and collaboration issues are addressed, and there are better outcomes for all involved.
Case study
Part 1. The Productivity Platform – a dual management operating system
Traditional mining operations function by allocating work to departments with clear reporting relationships and using planning, budgeting, job specifications and performance management systems. This system is efficient, but not ideal for handling highly interdependent and variable environments such as mines. There needs to be another system running in parallel to deliver the agility and coordination that is missing.
At Stratflow, we have developed a dual operating system we call the Productivity Platform that delivers the missing functionality (agility) without detracting from the benefits of a traditional hierarchy. The Productivity Platform is based on TOC principles and Dialogic Organisation Development, and fits into the current management system with minimal interference while reducing the overall workload.
The TOC provides the theoretical underpinning to enable managers and employees to use the best of current management theory to replace the parts holding performance back and to reap benefits previously considered unachievable. Because the Productivity Platform focuses on changing the way people think to better align with the reality on the ground, significant results appear very quickly.
Since 2000, in more than 80 interventions, the methodology has delivered output increases of an average 20 per cent (using the same resources) by creating a stable change platform from where improvement initiatives can be optimally targeted, sequenced and successfully implemented. (Blakemore and Lourens, 2017).
The Productivity Platform makes the overall goal of the system clear. It identifies and communicates the role of each person and department, and changes the management paradigm to one where we manage the overall system for greatest effectiveness. More time becomes available and there is no need to force work through the system faster than it can safely handle it.
The Flow Room
The ‘Flow Room’ is the place where the heads of departments, middle managers and selected employees get up-to-date visual information on what is happening across the business. Setting up a Flow Room means that teamwork will occur across layers and functions. Colour codes identify where attention should be focused and where help from support functions, such as HR and maintenance, is required.
The Flow Room moves the company out of firefighting by highlighting problems before they occur and putting in shock absorbers (buffers) to handle variation and interdependence.
Management and workers simultaneously become aware of problems in the system, and bottlenecks can be addressed on the spot. When a department or group needs help, it is clearly seen, and colleagues support them. These changes come as a great relief to workers and enable them to increase their engagement. As workers start to experience success, sometimes for the first time in their careers, they become accountable and begin to volunteer their energy and talents, reducing the load on management.
Before and after
Figures 1 and 2 demonstrate the impact of reducing variability on run-of-mine tons. The yellow line represents proven system capacity.
Figure 1. Average production 60 per cent of capability.
Figure 2. Average production 80 per cent of capability.
Part 2: Fewzion work management and short interval control software
Fewzion is an integrated frontline work management and short interval control software solution, developed by Commit Works, that replaces manual systems such as spreadsheets and whiteboards that are still widely used in mining operations. It is an easy to use operating backbone which allows frontline workers to:
- connect the work of the frontline to the intentions of managers and engineers
- avoid reasonably foreseeable mistakes that cause waste and poor performance
- hit targets and guidance more often.
This reduces variability, helps identify bottlenecks, improves average performance and helps mines achieve big improvements without spending significant capital.
Case Study – ‘No half measures will do’
At one mine we consulted to, headquarters had handpicked the new management team to guide operations. They made a point of choosing leaders who had a deep appreciation for the efficiency and control a good management operating system (MOS) could deliver. That might seem like table stakes for any well-run mine, but for this site it was a particularly high priority. Operations had reached an inflection point with a system built on too many spreadsheets that was undermining production, creating far too much waste, inefficiency and conflict. What’s more:
- Plan-execution discipline among teams was poor, as were levels of engagement
- There was no agreed-upon production plan or short interval control
- Longwall – their prime production source – was well below benchmark performance
- Development rates lagged behind longwall production rate, creating a negative longwall ‘float’.
For the mine leadership, the end goal was to leverage the incredible potential of the entire team, the valuable resource being mined, and surge productivity.
Drive change, trust and engagement
In April 2017, and based on a recommendation from a well-known consultancy firm, the mine engaged Commit Works to examine the business through the key lenses of planning, execution, and reporting – all to eventually be driven by Fewzion.
The project had three main objectives:
- Improve production and development rates, and reduce production variability.
- Improve communication and team coordination in every shift.
- Implement and sustain an effective management operating system (MOS) that drives change and future performance.
Over four weeks on site, Commit Works collaborated with the client’s project team to conduct a series of interviews and workshop with employees at all levels to uncover gaps in processes, visibility, and communications. They also extensively monitored production and reporting to determine the clearest and best KPIs across operations and the project’s return on investment.
What the combined team learned would drive the implementation and integration with existing platforms, inform the change management program Commit Works would deliver, and allow them to make sustainable recommendations for planning execution and reporting.
Related content:
Recovering losses with Fewzion
By July 2017, after an additional month-long implementation that included intensive Commit Works-led training and coaching for all users, Fewzion was live, fully integrated, and running the mine’s operations. Twelve weeks after the go-live, Fewzion helped drive a 51 per cent increase in operational hours, and delivered a 41 per cent increase in the average weekly development advance – essentially recovering the negative longwall float. The mine team has seen a remarkable lift in engagement owing to clearer processes and KPIs, plus a scheduling system that provides high visibility giving everyone ownership in operations.
The system is still in daily use across the site despite changes of ownership and leadership.
Conclusion
Variation in mining is – and will always be – more pronounced than in other industries such as automotive and manufacturing. Because of physical constraints in mining, the actions of any mining department can affect the work of all others. This creates interdependence, coordination and trust problems, which multiply the negative impact of variation on throughput.
It is possible to quickly (within 3-5 months) improve output, productivity and safety when we adjust our thinking and actions to harness and better manage variation. We have seen clients dramatically improve their productivity (typically more than 20 per cent but substantially bigger increases have been observed) and become safer work environments by using software and holistic management practices. These make work visible and change the focus to be forward-looking instead of analysing the past. Execution and planning become properly integrated and much more effective.
While these practices are innovative from a technical aspect, they succeed because they provide frontline leaders and workers the opportunity to build a community of trust and coordinate along with a unity of purpose.
Successful workers and frontline leaders who experience mastery, autonomy and purpose become highly engaged and deliver even better results. It is easy to lead well in such an environment. Employees, managers and executives experience lowered levels of stress and find joy in their work environment again. This is what has been missing in mining for many years.
Executives, after implementing the actions described often comment along the following lines ‘…I am happy with the improved financial performance in such a short time, but I am even happier with the kind of organisation we have become. I see teamwork and increased motivation everywhere.’
References
Lourens H and Blakemore J, 2017. ‘Turning mining performance around: From efficiency to effectiveness’, Australian Mining Magazine, May.
Tendon S and Mueller W, 2015. Hyper Productive Knowledge Work Performance, 368 p (J Ross Publishing)
Paul Moynagh and Glen Britton, Improving Trust and Commitment in Mining Operations, AusIMM UG Operators Conference, 2017
About the authors
Hendrik Lourens
Hendrik Lourens is the owner of Stratflow, a company that provides solutions to mining companies that are looking for immediate and significant results. Stratflow solves its client’s problems by enabling them to reliably meet production and cost targets, while improving on safety, lowering stress levels and becoming more innovative.
Hendrik has qualifications in Physics, Polymer Science, and an MBA. He has worked at Director level in manufacturing businesses and for a number of Tier 1 companies. On completing the “Managing the Theory of Constraints Way” in 2010 he became the first practitioner to pass all exams involved in the TOC Body of Knowledge within one year. His focus is on applying Complexity Science & Theory of Constraints to deliver breakthrough results. He has turned around manufacturers and improved the safety & productivity of mining and construction companies as well as published in various journals on efficiency and innovation.
W: Stratflow.com.au and miningdifferently.com
E: hendrik@stratflow.com.au, hendrik@miningdifferently.com
Paul Moynagh
Paul is CEO and a founder of Commit Works, making software for rapid, sustainable, improvements in productivity. Their suite of connected, frontline productivity solutions is designed to replace the disconnected cluster of manual whiteboards, paper and spreadsheets used in managing day to day operations.
These tools combine to form a “Frontline Commitment System” that enables teams of people to commit to and execute the right work at the right time, right across the site. Experience has shown that this improves productivity by over 20% on most operations whilst also reducing variability.
Paul has a Masters in Technology (Quality Systems) and over 20 years experience helping operational businesses improve productivity. He has both theoretical knowledge and significant practical experience delivering improved performance in complex operations. He has experience in mining, manufacturing and finance industries and has a passion for designing systems that improve performance.
Related content:
Would you like to understand, influence and drive your site’s management operating system (MOS) as a key deliverable in translating corporate strategy into site implementation priorities? Explore AusIMM's The Mining System short course, part of the Mine Operations Managers Core Skills series.