Innovation in mining
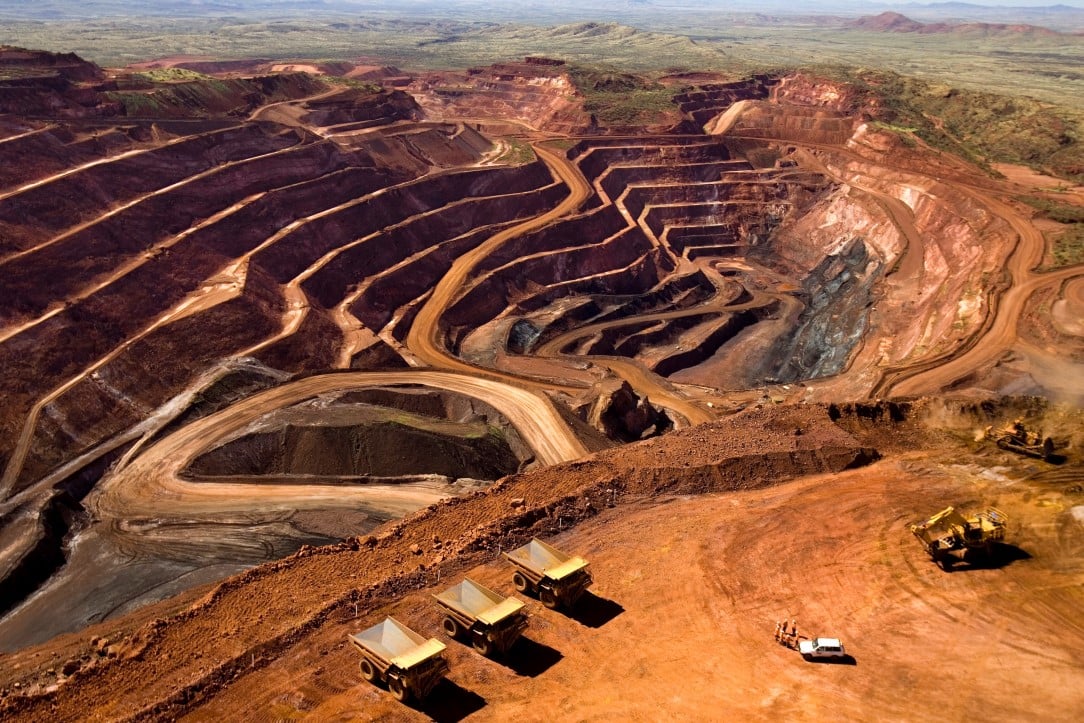
This article was published in 2015.
Are we different?
The title of this article is deliberately ambiguous. By ‘we’ do I mean ‘we in the mining industry’ or do I mean ‘we in Rio Tinto’? In this article I hope to show that, whichever definition of ‘we’ you choose, the answer would be yes.
Let’s talk about ‘we’ in the mining industry first. To begin with, it is my firm belief that innovation in mining is fundamentally different from innovation in many other industries.
Mining is often criticised as an industry where innovation and technological changes are resisted and implemented very slowly. A spate of recent reports characterise the mining industry as having ‘an accumulated deficit of transformational innovation’ (Ernst & Young, 2014) and remark upon ‘the lack of innovation in mining’ (Visser, 2013). It is a constant refrain at conferences that we miners are technically conservative and risk averse, blithely ignorant of the technological wonders that could revolutionise our industry overnight.
Is this true? Are we as an industry slow to innovate? The evidence would suggest that this common perception is at least partly true. Despite centuries of technological development, the mining industry still goes about its business in pretty much the same way as it always has. We smash rocks and haul the fragments away. Our machines have become larger, our equipment more sophisticated, but many mining operations today would be completely familiar to someone suddenly transported to our time from 50-100 years ago. In contrast, a time traveller like this would be completely lost in a modern office, factory or even some homes, where technology has completely changed the way we work and play.
It is often stated that there are a number of intrinsic features of mining that make technological changes difficult: we work in remote areas, we deal with extreme hazards and we work on a huge scale. While this is true, I do not believe that these factors alone are the reason for slow innovation. Mining resembles military operations in these aspects, and nobody would claim that an army of 50 years ago would resemble one of today. Remote areas, hazards and scale certainly multiply the difficulties with innovating successfully but they are not the fundamental reasons for these problems.
Instead, I think that a combination of three factors has caused mining to lag behind other industries in deployment of new technologies – namely failure, success and information.
Failure
Let’s consider failure first. Mining is inherently a risky business. With new mines, despite our best efforts, it is often not known precisely what is going to come out of the ground, or how it is going to behave in a plant, until operations actually start. Furthermore, the profitability of a new mining venture depends largely on the price that will be obtained for the product – something over which we have no control. These risks arising from orebody uncertainty and product price and are further increased by the factors mentioned previously: remote operations, hazards (both to people and the environment) and large scale. For all of these reasons, and many more, the possibility of failure hangs over many new mining ventures. Most of us who have been in the mining industry for some time have an intimate and painful experience of real operational failure.
Mining is often criticised as an industry where innovation and technological changes are resisted and implemented very slowly.
As a result of these inherent risks, new mines are particularly bad places to try out new and unproven technologies. Compounding the known risks with unknown technological risks is unwise unless absolutely necessary. The demands of discounted cash flow mean that even minor operational delays caused by commissioning problems with new technologies can cripple the economics of a project if they occur shortly after start up. Most mining companies therefore sensibly stick to the tried and true in new mines unless the business case for a new technology is completely overwhelming. Unfortunately, only rarely do the business benefits of a new technology justify even a marginally increased risk of project failure. This necessary avoidance of unnecessary technical risk has led to a common culture of being a ‘fast follower’ in the mining industry – companies that proudly admit that they want to be the ‘first to be second’ in deployment of new technologies. To date, this strategy has been very successful for many mining companies.
Success
In some ways, success in mining can be as big a barrier to technology development as the fear of failure. Once a new mine is successfully and profitably operating with its tried and true equipment, the impetus for technological change can be relatively small. If acceptable returns are being generated with conventional technology, then justifying capital expenditure on new technology in these profitable operations can be very tough.
In fact, this is a component of a general improvement paradox which we often see in mining. When times are good, it is often not possible to justify technological improvements to an operating process because the down time cannot be paid for by the incremental benefit. The business is so busy making money that it is not possible to justify stopping it simply to make a little more. Unfortunately, when times are bad, the business cannot justify the increased capital investment that it needs to run at lower costs and higher efficiency. Attracting investment in a business that is showing poor returns at that point is very difficult. The net effect of all of this is that the mine starts with conventional technology and runs it though good and bad times until it absolutely doesn’t work anymore or is hopelessly obsolete. Short of serious crises or major developments, minor tweaks to operations and equipment are often all that happens technologically until the mine closes.
So if fear of failure causes us to start with proven (old) technology, and success causes us to stay with it as long as possible, then I believe that one other factor – information (or rather, lack of it) – is the overriding reason why we have stayed this way as long as we have. Mining has always been about information: knowing where to mine and where not to mine is what separates successful miners from everyone else. Unfortunately, mines have always been rather information-poor places. As we in the industry are well aware, we often would like to know much more about the ore bodies which we are mining. Despite all of our exploration and development work, our brilliant geologists and our sophisticated computer modelling, we often do not know what we are going to get until we actually dig it up. This lack of knowledge and the resulting uncertainty fundamentally limit our ability to plan and hamper our efforts to carry out the plans we do have. And when we encounter something unexpected, which happens frequently, all of our plans have to be remade. The net effect is that we often are forced to work with low resolution, approximate mine plans that we know are not optimal and that can only be intermittently updated.
Information
Compounding this lack of ore body knowledge is the extreme difficulty we have in knowing what it is that we have actually mined until quite long afterwards. This problem is due to the nature of our ores: they are solids, and solids are dreadful things.
Mining moves solids in truly colossal quantities: no other industry on earth moves solid material on the scale of mining. Unfortunately, solids are often extremely difficult to deal with. Solids are, by their nature, not homogeneous. They can vary immensely in composition and size, they segregate and they resist mixing. They stick when we don’t want them to stick, and they fall apart when we want them to hold together. Metering the flow of solids is extremely difficult; measuring the precise composition of a flow of solids is even worse. It is practically impossible to know exactly the composition, size and mass flow of ore at every part of most mining processes at all times. Plus, not knowing what or how much we have imposes firm limits on what we can achieve.
Despite similarities between the mining industry and the oil and gas sector, the latter has been able to attain a much greater degree of sophisticated control and technical advance primarily due to the fact that they are dealing with liquids and gases, which are much easier to meter, transport and analyse than solids.
Historically, mining has evolved to deal with being information-poor in a number of ways. Our first line of defence is to average and blend. We take daily, weekly or monthly averages of things and work and report to these. When everything is blended and averaged, most of the noise goes away and things are much easier to deal with. Unfortunately much of the information is removed as well. The other thing we do is move slowly, in low resolution and in large chunks that are unlikely to be very wrong – especially when averaged. Finally, we handle disruption and chaos as part of our jobs. We deal with surprises, we don’t over plan and we are extremely adept at extricating ourselves from difficult situations. But these are really just coping strategies, and there is no doubt that if we knew more we could better plan and control, thus producing more at lower cost and lower impact. Innovating and changing the current course is difficult when we really don’t know what is actually going on and have very little ability to control it.
So if success, failure and lack of information make ‘we’ as mining innovators different from those in other industries, what makes ‘we’ at Rio Tinto different from other mining companies? How is Rio Tinto dealing with these challenges in ways that are different from others in the mining industry?
The Mine of the Future
About seven years ago, Rio Tinto realised that the revolution in information and communication technologies had reached a level such that the complex and difficult operational problems of mining could finally be tackled with some hope of success. As a result, Rio Tinto made the strategic decision to become the leader in mining innovation and reject the fast follower strategy of its peers. The resulting launch of the Mine of the FutureTM program has led to significant and sustained technological investment in a number of areas, some of which are widely apparent, such as the autonomous trucks currently operating in the Pilbara.
One of the first key areas of focus for the new Mine of the FutureTM program was to substantially increase the information available to mine operations. Note that information is not the same as data. Many mines generate a great deal of data; their generation of information is often much less impressive. A good definition of information is that information is the answer to a question. Unless the mine data can be used to answer questions, it is not information as such. Turning data into information takes systems, processes, and above all, analysis.
Mine Automation
As a core enabler for turning mine data into information, one of the first components developed within the new innovation strategy was Rio Tinto’s Mine Automation System (MAS). MAS functions as the information backbone for Rio Tinto’s mining operations, allowing data from all of the disparate mine sources to be integrated into one overall whole. It also allows us to apply mathematical models and visualisation tools that let users interrogate and integrate a wide array of data sets, providing novel insights that could not be obtained otherwise.
Building on this philosophy of converting mine data into information, Rio Tinto’s Operations Centre in Perth now directly controls our iron ore operations in the Pilbara, 1500 km away. In addition, Rio Tinto has developed a network of Excellence Centres in Brisbane and also in Pune, India which allow remote experts to study exactly what is occurring in processing plants and mine operations around the world. Insights gained from this deep analysis of mine operations can now be used to justify the development of entirely new mining technologies, thus defeating the mine improvement paradox. In fact, with more automation in place, many mining improvements are now actually software upgrades, which can be deployed much faster, at lower capital cost and at lower risk than hardware purchases.
Any new technologies that are developed, whether they are software upgrades or new hardware developments, continue to be thoroughly de-risked prior to deployment. Rio Tinto Innovation can now develop and simulate new Mine of the FutureTM technologies prior to trials in the Quarry Test Site near Perth. Successful trials at this facility are now leading to successful deployments of new, but proven, technologies in both existing and new mines.
Conclusion
So, to take the point made at the beginning of this article – that a modern mine site may look the same as that from 50 years ago – I want to emphasise that it is precisely what you do not see at a Rio Tinto mine that makes today different from back then. You do not see drivers in trucks or operators on drills. You do not see the web of communication infrastructure that transfers information to and from each component of the mine. And you do not see the people 1500 km away in Perth, or 10 000 km away in India who are analysing all aspects of the process, continuously learning and relentlessly driving improvements to the business.
For a variety of reasons addressed in this article, innovation in mining has historically been very different from many other industries. Having made and sustained strong technological investment over the past seven years, Rio Tinto is now reaping the benefits of higher productivity and accelerating technological development which we expect will continue quickly in the years to come.