5 minutes with Gavin French, speaker at MineVent 2022
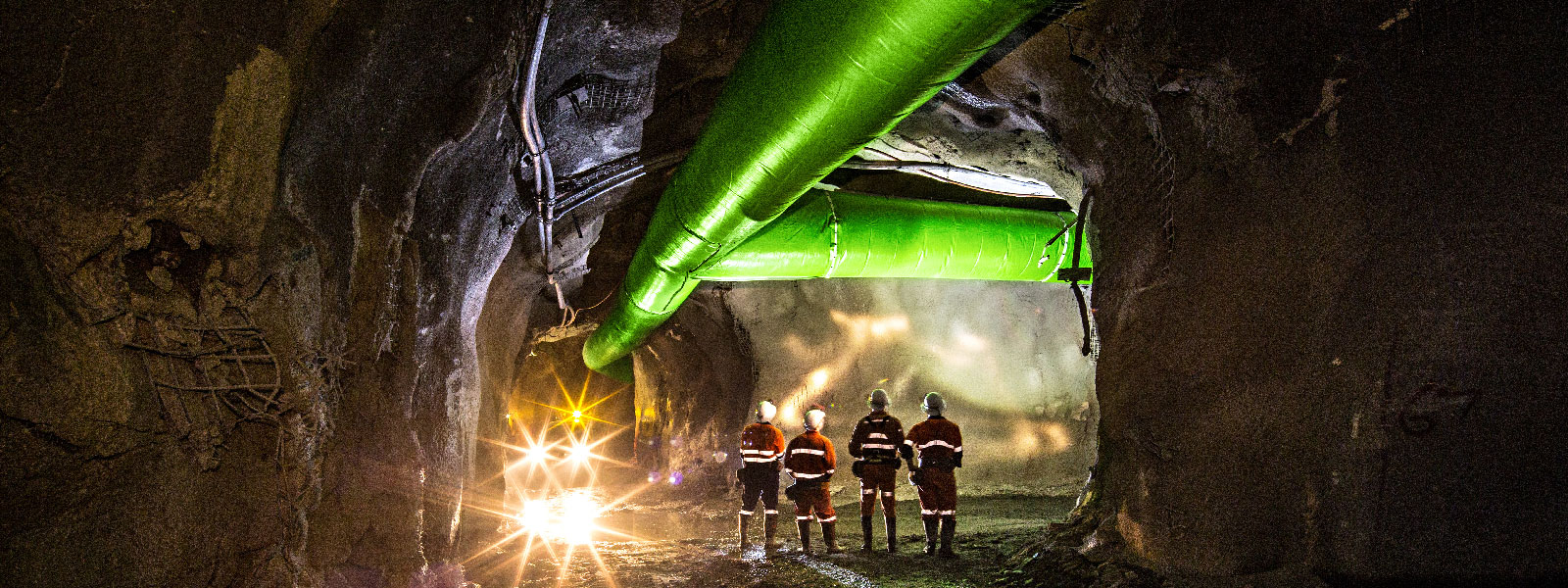
This year's Australian Mine Ventilation Conference 2022 will be held on the Gold Coast from 10-12 October.
We sat down with speaker Gavin French (pictured), State Sales Manager & Australian Product Champion Fiber Sensing at Yokogawa Australia and New Zealand (an AusIMM Industry partner), to discuss his Mine Vent 2022 presentation on ‘Real time thermal monitoring of underground coal mines using fibre optics’.
Can you explain a little bit about how the project in your presentation came about?
Yokogawa for many years provided the mining industry with innovative and diversified solutions to the problems they encountered. We were contacted via the site Electrical Engineer with an urgent request to address a heating event that occurred only a few months earlier. It is understood the governing Mining Safety Department was very clear that our client needed to demonstrate the use of innovation to remove or mitigate the possibility of such an event happening again. Along with innovation came a need for real-time monitoring, and the underground environment posed some real challenges for the Yokogawa engineers. Having seen the product previously our client was aware of such technology but not sure on how it could be applied to solve their problem nor whether Yokogawa could deliver a solution to meet the needs of all the stakeholders.
What were some of the challenges from executing the project, and how were these overcome?
Firstly, time was of the essence, and we needed to collaborate with key partners quickly to engineer a robust and transportable solution. We were also able to deal directly with the Yokogawa factory in Japan and they saw the need for a quick turnaround managed correctly and all the key partners did their job well and delivered within the requirements. Secondly, the challenge was the need for the system to not only provide real time and accurate monitoring, but also be totally flexible and operated from a portable gas monitoring trailer. The flexibility solution was done through the incorporation of specific “tactical” rated connectors that were built to withstand harsh environments and the use of tactical fibre optic cable that can withstand not only direct impact from above ground mining equipment but also being vertically suspended long distances down boreholes.
The use of fibre optics in this way is a new approach for underground mining. Do you think we will start to see more widespread use of the technology?
We were able to recently gain support from Glencore in the use of such fibre optic in underground applications. So yes, we think there will be a groundswell of companies looking for the benefits of conducting real time temperature measurements. The technology can be applied equally to not only the different types of underground mining but also for equipment and infrastructure. Once we pass the early adopter stage, I think we will see the bulk of miners looking to incorporate the technology into their everyday operations. Bringing co-innovation into the solution means that we are simply a partner in the way companies use such technology. Others will see the need to innovate and given every site has a different set of challenges, we are well poised to discuss, design and deliver a long-term solution of real time thermal monitoring of any sized operation.
Could this technology be combined with other new or existing technologies to further improve safety of underground workers?
Absolutely. On the one hand we have the one thing not currently addressed and that is that the system is flexible enough to not only be used for its current application but also to be expanded to be used around machinery and personnel. Think about every part of a mine being monitored for subtle changes in temperature, transformers; moving equipment, rotating equipment, cutting equipment all being monitored for changes in temperature as low as 0.03 degrees Celsius.
On the other hand, it can be used in conjunction with existing mining safety control systems. The pedigree of the DTSX (Distributed Temperature Sensor) is that it was designed and built around platforms shared with the Yokogawa DCS, or Distributed Control System. Yokogawa can achieve any required output including Modbus/TCP (Transmission Control Protocol) or even Distributed Network Protocol 3 (DNP3) to feed directly into an existing control system. The underground mine that used this technology were also able to bring their two gas monitoring systems down the boreholes with the sensing cable. Doing this the cabling system gave physical support to the monitoring pipes, thus improving the life of the mobile equipment and ultimately the safety of the workers.
What are you most looking forward to at Mine Vent 2022?
I am looking forward to learning from the delegates the challenges they have in their working environment and coming up with an innovative solution to solve these issues. Engagement by Yokogawa will be built around the co-innovation, and I am also really excited to call on our extensive resources within the team here and abroad to solve any challenges presented. As mentioned before learning from the other delegates will also help us to best build a solid understanding of their challenges and from understanding comes a quality solution that will exceed their expectations.
Not only am I excited to learn from delegates, but also from the other exhibitors, learn their challenges and see if Yokogawa can offer a long-term solution.
Lastly, I am looking forward to educating delegates that Yokogawa is simply not a product manufacturer but actually a complete solution provider dedicated to risk reduction and life preservation.