Technology and innovation in mineral processing
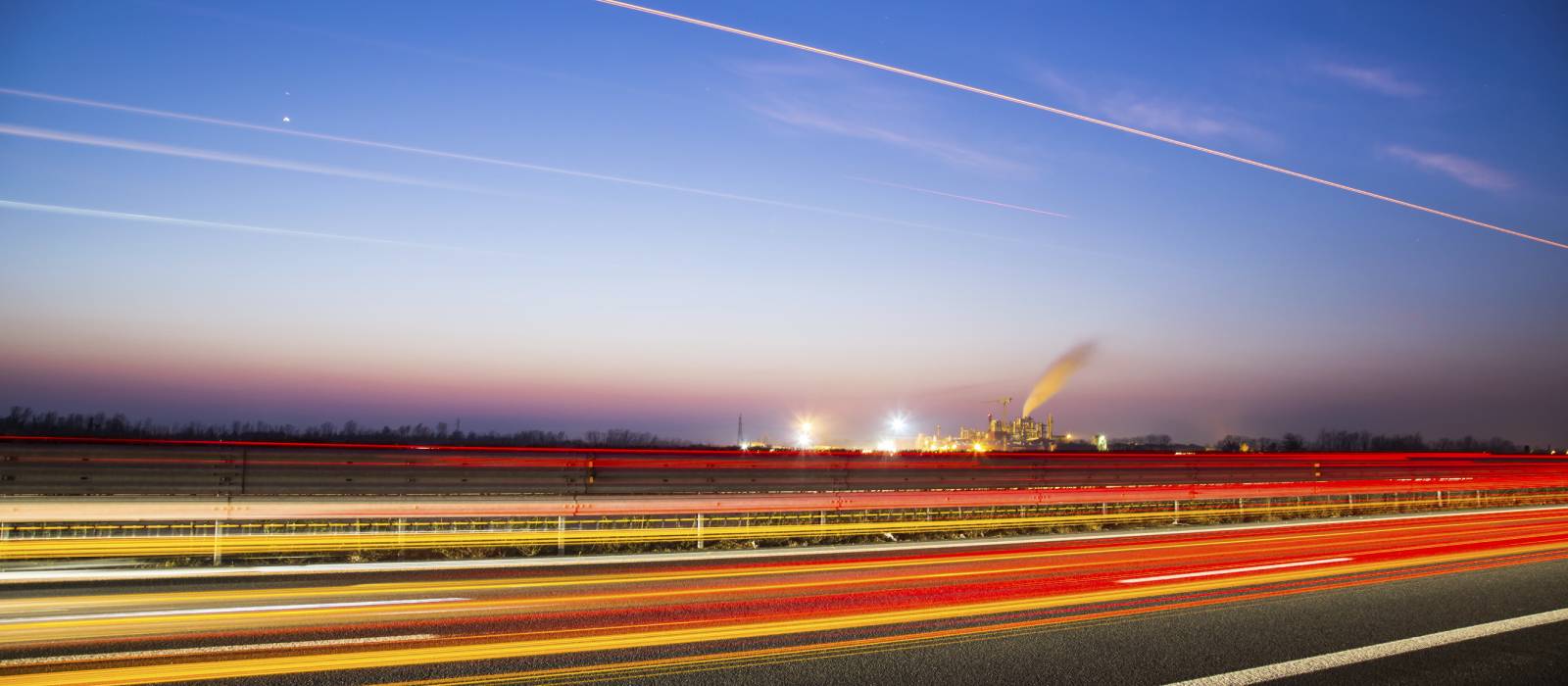
A reflection on recent progress in mineral processing technology, and the factors that help drive new and disruptive thinking
The pace of change in mining technology – and more specifically, in minerals processing – mirrors society as a whole. The demand for minerals is driven by a society that is adopting new technology at a rapid rate, with the changes in technology driving the changes in demand for minerals.
The industrialisation of Asia – in particular China and India – is driving demand for construction and fabrication metals such as steel, copper, zinc, lead, gold and silver. This is supercharged by the demand for newer ‘battery materials’ such as graphite, lithium, nickel, cobalt, and other historically minor metals/materials.
As a result of improvements in technology, it is now easier to monitor, measure and act on performance indicators to reduce energy consumption and improve minerals processing efficiency. This short paper summarises some recent changes in technology and addresses the following philosophical and strategic questions:
- what is the intrinsic relationship between technology and innovation?
- is Australia a global leader in this space, and how do we foster a culture of innovation in mining?
- is it the innovation of people that develop new technology, or technology that enables innovative ways of operating, or a combination of the two?
The intrinsic relationship between technology and innovation
Most technologists will agree that while there is a link between technology and innovation, the link is not unique. Innovation can be applied to many fields of endeavour, from the artistic to the philosophical to the material.
Innovation in technology pertains to the development of new ways to achieve a desired end, typically an improvement in quality or efficiency. The key here is that it is not innovation unless the new way actually works, that is, achieves the designed end and results in an improvement. There is an associated philosophical discussion as to what constitutes incremental change and what is true innovation, but that discussion is really only for the purists. For this paper, if the new way results in improved efficiency (reduction in effort) or improvement in quality, it is innovative.
Mineral deposits are generally becoming lower grade and mineralogically more complex. The mining industry has responded to this challenge by innovating and developing technologies that have increased efficiency and productivity, some through the increase in scale and capacity, some by challenging the norms of processing.
The current focus of innovation in mineral processing is on increasing production rates (with the same equipment), reducing capital and unit operating costs, and minimising energy, water and environmental impact. Pre-concentration technologies, more energy efficient comminution technologies and circuits, coarse particle recovery, and storage of dry-stacked tailings are examples of areas where significant fundamental innovation is impacting on process plant design.
There is no doubt that the adoption of new technology that resolves a current problem is more rapidly and successfully adopted than a new technology that is developed for a potential that may arise. Need is the biggest driver of innovation in mineral processing.
Fostering a culture of innovation in mineral processing in Australia
Australia has had a strong focus on primary industry over the past 200 or more years. An important part of this has been the mining and processing of minerals for ultimate metal production (mostly overseas). It is an interesting cultural development that Australians have an open, and sometimes blunt, approach to challenges, be they social or material. Australia’s history of gold, iron ore, base metals and coal mining and processing, augmented by numerous other historical and emerging value metals/materials, has facilitated a history of innovation across a wide range of mineral processing activities. These include, to name but a few:
- the development of flotation at Broken Hill
- the adaption and improvements in carbon-in-pulp/leach processing in Western Australia
- improvements in electrowinning technology by Mt Isa
- the development of IsaSmelt/AusSmelt
- new and radically different styles of flotation cells
- new assaying methods by the CSIRO (historical and recent)
- effective and efficient engineering and design approaches, particularly as applied to gold processing plants in the late 1970s and 1980s.
The nexus of the Australian “open approach” and a history of technical development has led to significant global penetration of Australian influence in innovation in a number of mineral processing areas. Three examples are:
- the promotion of energy efficient comminution circuit design by the Coalition for Eco Efficient Comminution (CEEC)
- the development and adoption of energy and water efficient copper concentrator designs
- the development of cost-effective gold plant and copper concentrator designs.
CEEC has a global reach with an Australian centre of operations. Its purpose is to raise awareness of research findings, alternative comminution strategies and installed outcomes by accelerating the distribution of information, knowledge and technology transfer. The ultimate objective is to lower processing costs and raise shareholder value, as a result of improved comminution practices.
The developments in copper concentrator design have focused on separating minerals at coarse particle sizes, thus avoiding the energy input in comminution and reducing the water that is bound up in fine tailings disposal, improving water efficiency. This is being achieved by developing bulk ore sorting and coarse particle flotation technologies that result in coarse waste streams that can be more efficiently stored. Cadia, in NSW, installed some of the first bulk ore sorting technology and the first commercial Hydrofloat™ coarse particle flotation machine. In parallel, strategies for safer tailings disposal, including dry stack filtered tailings and co-disposal with mine waste, are also resulting in better environmental outcomes, sometimes at lower cost.
Australian engineering companies ‘learnt their trade’ in the late 1970s, competing with the larger North American based engineering companies in the then emerging gold mining boom. The Australian engineers were innovative and cost focused, adapting to a lump sum turn-key project delivery approach. They went on to dominate the construction of most of the gold plants built in Australia before taking their ideas overseas (Close, 200). This design approach has further developed and fed into the design and construction of larger copper concentrators in Africa, Asia, South America and North America over the past 15 years (Lane et al, 2008; Lane and Dickie, 2009; Lane 2019).
Australians foster innovation through their inherent cultural behaviour and the willingness to challenge norms and authority. This combines with an abundance of mineral resources and the need to market commodities globally, where metal prices are seldom stagnant and often low at some stage in a given decade. Whilst there is some government support for research and development in mineral processing, this is insignificant when compared with the value of the potential efficiency improvements.
People and innovation
My first reflection on the question ‘Is it the innovation of people that develop new technology, technology that enables innovative ways of operating or a combination of the two?’ is that all innovation is driven by people. But there is an influence on people in mineral processing from technology developed outside the mining industry. In this way, new technology is enabling innovative thinking in mineral processing.
As examples:
- New instruments/sensors and advances in control system configuration are facilitating higher levels of automation. This is enabling improvements in process monitoring and process stability, which ultimately enable incremental changes that further improve performance.
- Community expectations around a mining company’s ‘licence to operate’ are continually changing, and this is driving the need to use water and energy more efficiently and reduce the impact of mining operations on the natural environment. The impact of these changed expectations is driving how mineral processors assess the ‘best’ process and balance the risks associated with new technology and the advantages of reduced environmental impact.
In conclusion, advances in new technology and the innovative thinking that accompanies these advances need drivers. The advances in technology during war or space race(s) exemplify this in the general community. However, innovators have the capacity and ability to identify constraints in existing thinking or processes and simplify the problem to generate a new solution that often has the potential to disrupt existing business. It takes a mix of insight, courage, ability, focus and ultimately the ability to influence that is not the norm in a community of one person.
George Bernard Shaw postulated that a reasonable man adapts himself to the world, whilst the unreasonable man persists in adapting the world to himself, and therefore, all progress depends on unreasonable men (or women). By inference, a good manager needs to truly include ‘unreasonable’ people in their team to encourage innovation.
References
Close S E, 2002. The Great Gold Renaissance (Surbiton and Associates:Melbourne)
Lane G, Staples P, Dickie M, and Fleay J, 2008. “Engineering Design of Concentrators in Australia, Asia and Africa – What Drives the Capital Cost”, Procemin 2008, Santiago, October
Lane G and Dickie M, 2009. “What is Required for a Low Cost Project?”’ Project Evaluation 2009 Conference, Melbourne, AusIMM, April.
Lane G, 2019. “Lessons Learnt from Smaller Projects Applied to Big Projects – Surely it Must be Easy?”, MetPlant 2019, AusIMM