The state of safety culture—how does mining stack up?

New study reveals key opportunities for driving a positive safety culture in the mining sector
Only 11 per cent of mining sites operate in a positive safety culture, according to a recent cross-industry study of more than 21,711 participants. For organisations whose sites fall into the remaining 89 per cent, operating in a negative or unhelpful safety culture could be detrimental to safety outcomes and increase the risk of serious incidents and fatalities.
Conducted by safety culture expert Sentis, the study has highlighted the key strengths and areas of opportunity for organisations seeking to improve their safety culture. The study – which analysed more than 21,711 employees’ perceptions of safety culture—has uncovered trends spanning industry. And while the research suggests that pockets of excellence exist, there is certainly room for improvement when it comes to driving a positive safety culture across the sector.
Why maturity matters
It makes sense that safety culture influences safety performance and is a significant factor in predicting the likelihood of safety incidents. But what does it really look like? And how can you tell if a safety culture is positive or negative?
Safety culture refers to employees’ attitudes, values and beliefs about safety in the workplace—including the implicit safety rules or guidelines present at the frontline—while safety culture maturity describes the journey organisations take as they progress towards safety excellence.
On this journey, organisations possess different profiles of safety culture, each differing in their level of maturity or effectiveness. So, it stands to reason that the maturity of an organisation’s safety culture will influence whether safety outcomes are overarchingly positive or negative.
The dangers of a negative safety culture
A negative safety culture is driven by shared attitudes and beliefs that are unhelpful. In these types of cultures, safety is seen as a burden, a waste of time or something that gets in the way of getting the job done. Ultimately, safety is viewed as something that is imposed by leaders or the organisation, rather than coming from a place of internal motivation.
As a result, compliance with safety processes, rules and procedures is sporadic and often depends on a leader watching, monitoring and enforcing performance. Typically, this manifests in a culture where workers:
- take a ‘tick and flick’ approach to safety
- only comply with safety procedures when being watched and monitored
- cover up incidents and errors
- cut corners and turn a blind eye to safety procedures they don’t see value in, during times of production pressure.
In this type of culture, it’s not a question of if an incident will occur, but when and how serious.
How mining stacks up to the cross-industry benchmark
The Sentis study included data from 73 organisational sites across eight core industries: agriculture, construction, government, healthcare, mining, manufacturing, oil and gas, and utilities.
When compared to the broader research benchmark, mining performed poorer than the average, with 89 per cent of sites operating in a negative safety culture (ie either Counterproductive or Public Compliance levels of cultural maturity – See Figure 1).
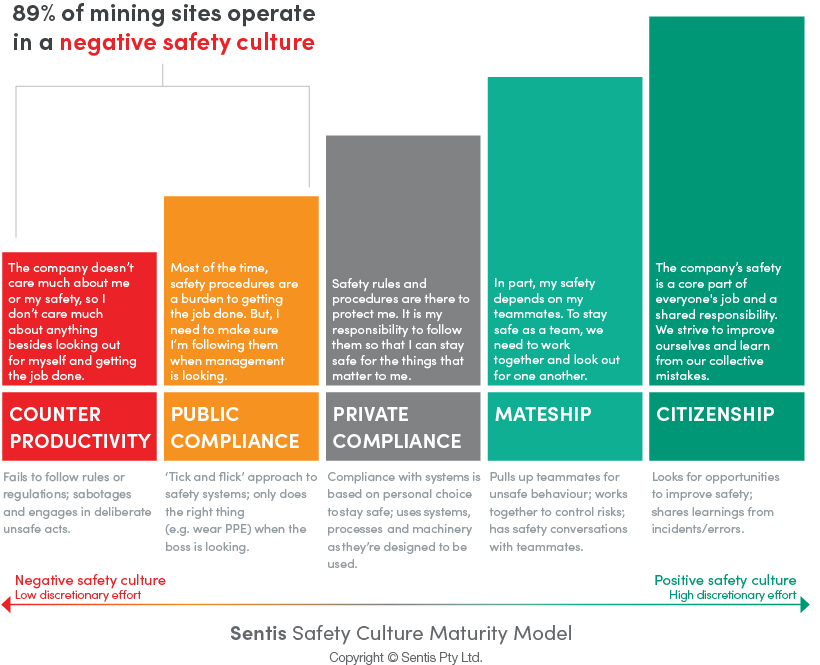
However, the result that is most alarming is the high number of sites sitting at the Counterproductive level (18 per cent), representing a significant and immediate risk to the safety of workers on these sites (Figure 2).
How to spot a Counterproductive culture
According to the study, in a Counterproductive culture, employees may actively work against the company and existing safety rules and procedures. Or in some cases, it may be that safety systems and processes are insufficient or that employees simply haven’t received adequate training on how to use them or why they are important. Often employees' actions in a Counterproductive culture are driven by the belief that the organisation doesn’t care about their safety, so they will just do their job and look out for themselves.
Characteristics of a Counterproductive culture include, but are not limited to:
- negative or dismissive attitudes towards safety
- a lack of safety conversations taking place
- workers complain that procedures are impractical, unclear and only there to control them
- production, efficiency and/or quality take priority over safety
- maintenance is reactive and only happens when equipment failures hold up production
- leaders are rarely seen onsite, except to police production.
It’s clear that a safety culture transformation is needed in the industry, but where should organisations start?
Top opportunities for organisations seeking to improve their safety culture
According to the study, there are five key areas of opportunity for businesses seeking to shift towards a more positive safety culture.
1. Safety procedures need to be reviewed for clarity, accuracy and usability
A common gripe for study participants was that safety procedures are either too complicated or difficult to implement. This, coupled with a perception that safety procedures are more about protecting the company from potential legal action than workers’ personal safety, led to disengagement and devalued the importance of procedures in the eyes of workers.
Helping workers to understand that procedures are tools that help them to stay safe for their own benefit can be tricky, especially when an ‘us versus them’ mentality is deeply embedded. Reviewing safety systems and procedures for clarity and accuracy and engaging workers in the process is a good first step. Taking a consultative approach helps to ensure that new procedures are practical, simple and easy to follow in the field, and helps to foster engagement and motivation.
2. Managers need to walk the talk when it comes to safety
Especially when the pressure is on and production is a focus, managers need to step up their game and walk the talk. Without effective role modelling of helpful safety attitudes and behaviours by managers, a disconnect erupts and poor perceptions of the organisation’s commitment to safety run riot.
Walking the talk means being visible and spending time in the field with workers—not to monitor them, but to engage with them. Managers need to consciously make it a priority to talk to workers, show interest in the day-to-day safety challenges that teams experience and support them to find a resolution.
3. Change needs to be managed better, no matter how big or small
It’s no secret that change is hard, but managing change effectively can be even harder. When change is managed poorly, workers can become anxious, withdrawn or hostile, disengaging with safety processes and displaying an increased number of unhelpful safety behaviours.
When it comes to change, communication is key. If workers feel like they have been consulted, or at the very least pre-warned about upcoming changes, they are more likely to be receptive and less likely to display change cynicism. It is important to remember that while leaders typically consider restructures, mergers or the closure of a site as major changes that require attention, small changes need to be managed, too. In the eyes of workers, changes to their routines, rosters or the way they do their job may also feel like major changes.
4. Workers need to feel safe and empowered to report incidents and errors
Accurate and timely reporting of safety incidents is crucial to achieving a positive safety culture. So why is it that so many workers fail to report incidents and errors? For the sites in the study, the reluctance to report stemmed predominately from fear of punishment or process issues. A lack of psychological safety and perceptions that incident investigations are akin to witch-hunts only served to fuel the cycle of underreporting.
Shifting the focus of incident investigations away from assigning blame and towards creating shared learning for improvement is a critical first step. Leaders should also focus on providing feedback following a report, ensure reporting systems and processes are user-friendly, and celebrate individuals and teams that report – especially when their report leads to an improvement.
5. Leaders need to practise effective reward and recognition
Leadership soft skills are often overlooked, especially at the frontline. Too often, leaders fail to consciously consider the specific behaviours they want to recognise in their team. This becomes especially dangerous when reward and recognition processes are tied to KPIs like incident rates and production goals. Rather than focusing recognition on the outcome (which may be inadvertently driving unsafe or counterproductive safety behaviours), leaders should focus their attention on helpful attitudes and behaviours.
Communicating to workers the values and behaviours expected of them, and how they relate to the company’s safety vision or goals is important, as is catching people doing the right thing and recognising them in the moment.
Access the full study and recommendations
Overall, it’s clear that there is a lot of work to do to shift safety culture across the mining sector. But change is possible, and the Sentis study offers the industry comprehensive, yet practical insights and recommendations for where to start.
The Sentis study findings are available in their latest report ‘Driving a Positive Safety Culture’. The report includes more than 60 individual recommendations for leaders—as well as a practical step-by-step roadmap for setting up a cultural transformation project for success—and is available as a free downloadable resource on the Sentis website.
About Sentis
Offering safety culture assessments, training, coaching and consulting, Sentis helps organisations to break through the safety plateau and achieve positive safety culture change. As experts in applied psychology and neuroscience, Sentis makes safety personal and equips employees with the knowledge, skills and motivation to make safer choices, each and every day. This leads to safer, more engaged workplaces, as well as increased productivity, leadership capability and transformational, sustainable safety culture change. Since the introduction of their pioneering ZIP program in 2003, Sentis has empowered more than 350 companies and 160,000 individuals to think differently about safety.