The strategic, risk-based approach to safety production
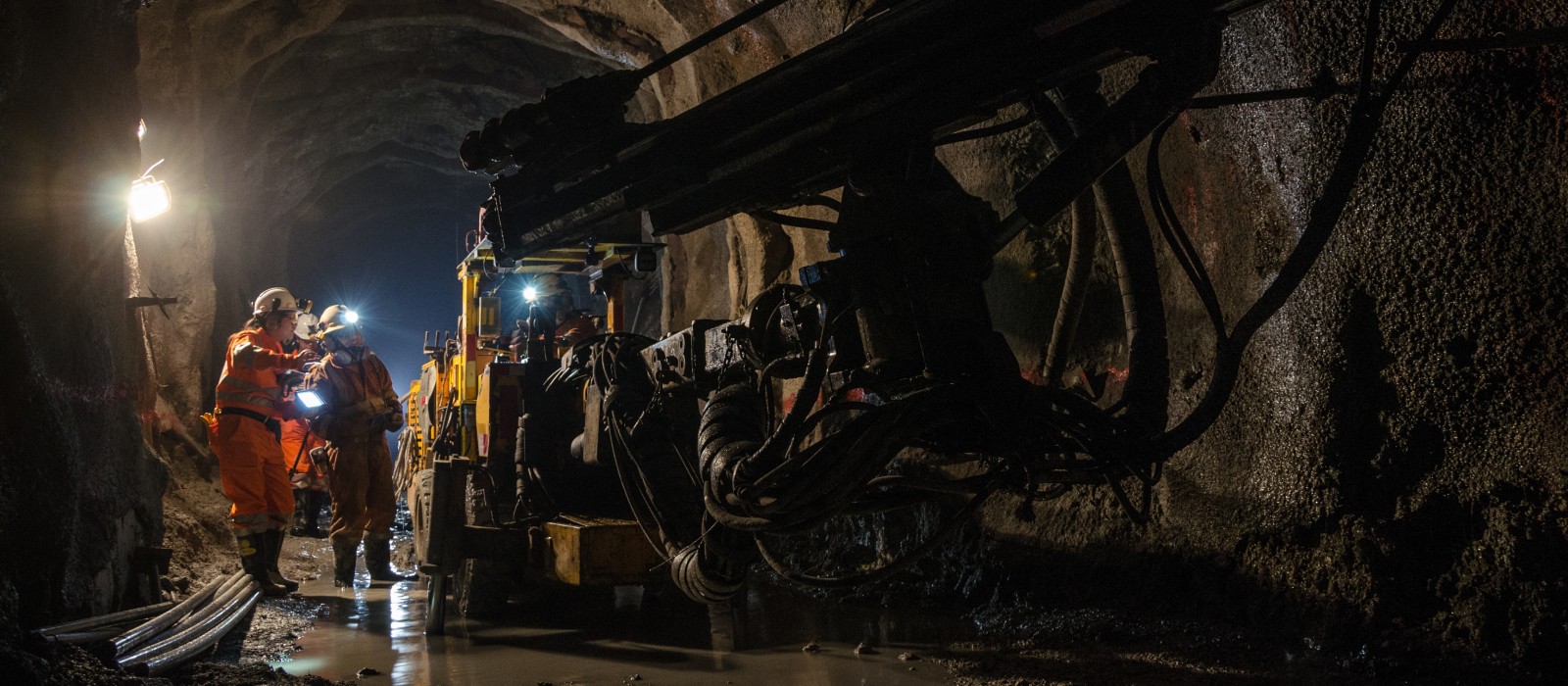
The risk-based approach to workplace health and safety (WHS) compliance has applied to the mining industry since the mid-1980s. Recent changes, particularly industrial manslaughter provisions, have raised serious concerns within the industry given the prosecutions of business owners resulting in prison sentences and significant fines (WA Business Owner's Jail Sentence; First Industrial Manslaughter Prosecution Queensland).
The changes to legislation stem from the shift to harmonisation across Australian jurisdictions based on ‘model’ WHS laws (Law and regulation | Safe Work Australia) with the biggest impacts being:
- the wider application of duty of care from the employer-employee relationship to any ‘Person Conducting a Business or Undertaking’ (PCBU)
- increased exposure of Company Officers to charges
- the requirement for more proactive practices to consultation with employees and contractors
- inclusion of psychological health with associated hazards (Modernisation of WHS Laws FAQ).
Concurrently in a broader context, there has been a shift from ‘safety-based thinking’ (practiced as a separate business function from production) to ‘risk-based thinking’. This is largely due to changes to International Standards (eg ISO 45001, 14001, 9001); the focus of risk-related disciplines (social licence to operate, quality, security, business risk); and the industry’s need for improved productivity without compromising WHS performance.
The missing piece amidst this increasing complexity is a clear understanding of the nature of risk. This gap in knowledge has resulted in what is known as the ‘bureaucratization of safety’ (The Bureaucratization of Safety) without recognising that effective risk management improves both safety and production.
WHS legislation acknowledges that risk cannot be reduced to zero, as explained by the principle of ‘reasonably practicable’ (Meaning of Reasonably Practicable); there is always a residual risk remaining after all practical controls have been implemented. Defining ‘reasonably practical’ includes considering what is known about hazards, the risk associated with the hazards, the means of controlling that risk and, importantly, the cost of mitigation.
WHS legislation provides a benchmark for minimum compliance. It does not provide the business case for effective risk management to ensure continuity of production and to mitigate losses impacting the bottom line. This is not the role of the regulator, and the mining industry has had sufficient lessons learned prior to and since the introduction of safety legislation to know that major safety incidents are highly detrimental to production and to business reputation.
One of the major gaps has been the over-reliance on lower order controls such as procedures and personal protective equipment rather than addressing the nature of risk. This current concept of residual risk has driven the assumption that more procedures reduce the ‘raw risk’ exposure of the organisation. However, these lower order controls are known to be unreliable in adequately addressing risk (NOPSEMA Complex Decision-Making). It is better to consider the residual risk after higher order controls such as elimination, substitution and engineering controls covering safety, efficiency and reliability in design, together with the quality of the systems used for production.
Visualising the nature of risk
To provide a more practical understanding of the nature of risk and the impact of uncontrolled risk on safety, production and work quality, Figure 1 has been developed to introduce the concept of ‘entropic risk’ caused by systems degradation. The Figure starts with the idealistic concept of zero risk in Section 1, where the organisation’s systems (work processes, technology, the physical environment and people) combine to achieve ‘perfect safety, production output and work quality’.
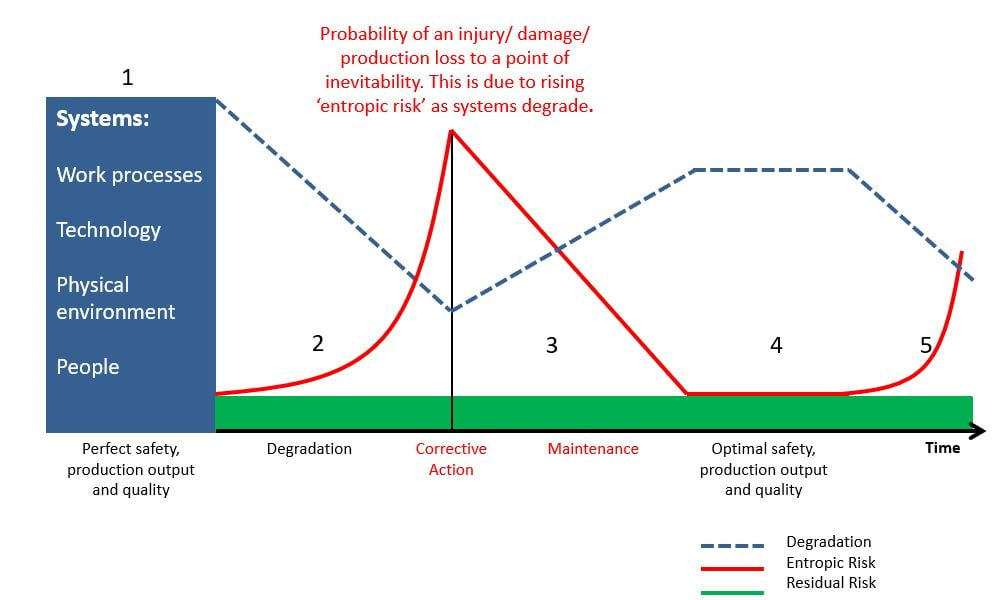
Realistically, industry cannot operate to this ideal. Section 2 shows that there is a residual risk (green) and that the four systems that the business uses to produce output, whilst contributing to the total residual risk, also tend to degrade (dotted blue line). This is evident in operations across all systems and includes such issues as workplace, plant and equipment wear and tear, lack of human factor reliability, plus procedural controls that do not reflect how the work is done. Concurrently with this degradation there is a rising ‘Entropic Risk’. The figure is illustrative rather than based on literal mathematical relationships because it is important to highlight that this entropic risk, reflective of an organisation shifting to a state of chaos, is incurring losses to production, safety and quality along the rising red line. The escalation of risk – if left unchecked – will result in significant loss(es) impacting the bottom line.
Throughout the five phases of the diagram, the residual risk remains the same because of financial and technological constraints preventing short-term additional risk reduction. In this approach, residual risk can only be achieved through improved ‘risk management in design’ – ie capital expenditure. This is the same concept as the inclusion of the cost consideration in the definition of ‘reasonably practicable’.
In Section 3, the business recognises the escalation of risk and takes corrective action thereby preventing a significant loss. To mitigate further degradation, proactive maintenance practices are implemented to improve the standard of the system inputs, eg scheduled maintenance of plant, equipment and the work environment, streamlining of procedural controls to improve reliability and standardisation whilst concurrently building the capability of the workforce.
In Section 4, the organisation has achieved ‘optimal safety, production output and quality’ through the effective management of risk. Notably when considering this residual risk, management do not assume that layers of further administrative and procedural controls have an impact on this risk but instead drive the decision process on the need to have quality systems in the first instance, to prevent degradation of those systems, and to manage the current level of residual risk inherent in their operations. Decisions and the culture are driven by risk management to achieve safety, production and quality work concurrently.
Management maintain vigilance with an awareness that standards can degrade. In the final Section 5, the organisation starts to lose operational discipline or is impacted by disruptive forces which cause entropic risk to rise again, resulting in losses to safety, production and work quality. Red flags may include WHS incidents, equipment breakdowns, re-work, failures in the supply chain and inability to maintain continuity of production at realistic targets. Overall, the figure shows that organisations can go through a cycle of degrading (2), mending (3), optimising (4) and degrading again (5). Larranaga (2013) refers to this concept as ‘Disaster Creep’ and states:
Many modern energy, industrial, transportation, health care, telecommunications, and political systems are highly vulnerable to small changes that propagate and develop into major disasters. This systemic tendency to unravel, decay uncontrollably, or move from order to disorder (eg disaster) is a characteristic of all natural and human-made systems and is defined by Newton’s Second Law of Thermodynamics as ‘entropy’. Before one can overcome this entropic tendency of all systems to unravel, one must understand the nature of system failure across multiple disciplines.
When considering both the present performance and horizon forecasts for the business, effective risk management entails focusing on the quality of system inputs, loss prevention and continuity of production. This approach also provides strategic direction for continuous improvement. Figure 2 illustrates the four steps required. These are:
- Take corrective action to address entropic risk caused by degradation of systems (reactive)
- Implement maintenance practices to prevent entropic risk within systems (proactive)
- Manage current residual risks (reactive and proactive)
- Reduce residual risk in the longer term through capital investments, innovation, standardisation and economies of scale (proactive).
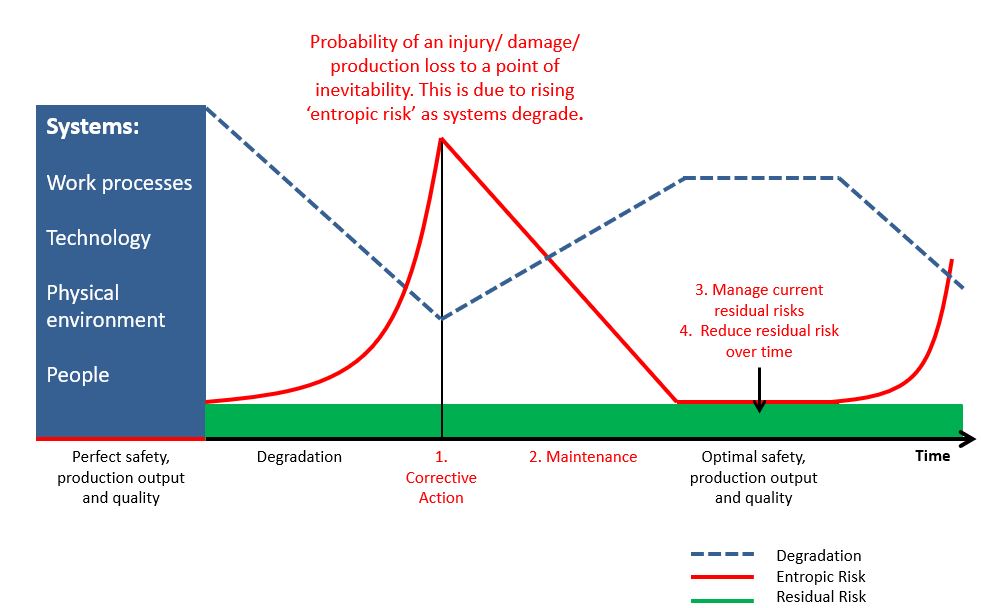
This strategic approach leads to a shift from ‘safety thinking’ to ‘risk-based thinking’. For instance, management of current residual risk means that the organisation must focus on potential critical failures. Under NSW legislation, for example, these include principal hazards such as fire or explosion, subsidence, spontaneous combustion etc. All such events are not just safety issues but business risks that could potentially result in force majeure. The new legislation is directing mining companies to address those risks that could result in fatalities, serious injuries and debilitating illnesses. From a ‘helicopter view’, these are also real risks for production in the immediate term and liability in the longer term. Within this broad perspective, effort spent on minor events pales into insignificance.
The key takeaways from this article are that there are two types of risk: residual risk and entropic risk which is caused by systems degradation. Both have a negative impact on safety, production and the quality of the work undertaken. The opportunity is to operate more strategically to pursue these objectives concurrently using WHS legislation as a minimum standard. All other matters that are not clearly prescribed in the legislation are subject to ‘reasonably practicable’ and that means that the solutions can be safe, productive and delivered in ways that have a positive outcome for stakeholders – management, workers and regulators.
The other key takeaway is to question the ‘state of play’ of the business and ask: where are we on this escalating entropic risk curve? Are we incurring losses due to poor quality systems or degraded systems? If so, how do we mitigate significant loss plus improve WHS, efficiency and work quality though better risk management?
References
Grieve, R. and Van der Stap, T., August 2020, Entropy – A Leadership Issue, Professional Safety Journal, American Society of Safety Professionals, USA.
Larranaga, M.D. 2013. “Issue 71: Disaster Creep – Why Disaster and Catastrophe are the Norm – not the Exception”. SFPE, http://www.sfpe.org/?page=FPE_ET_Issue_71
Mol (Van der Stap), T., 2003, Productive Safety Management – a strategic, multidisciplinary management system for hazardous industries that ties safety and production together, Taylor and Francis, Oxford.
Van der Stap, 2018, Chapter 29 Risk Leadership – A Multidisciplinary Approach, Safety Leadership and Professional Development, American Society of Safety Professionals, USA.