Shifting minds key to shift in mines
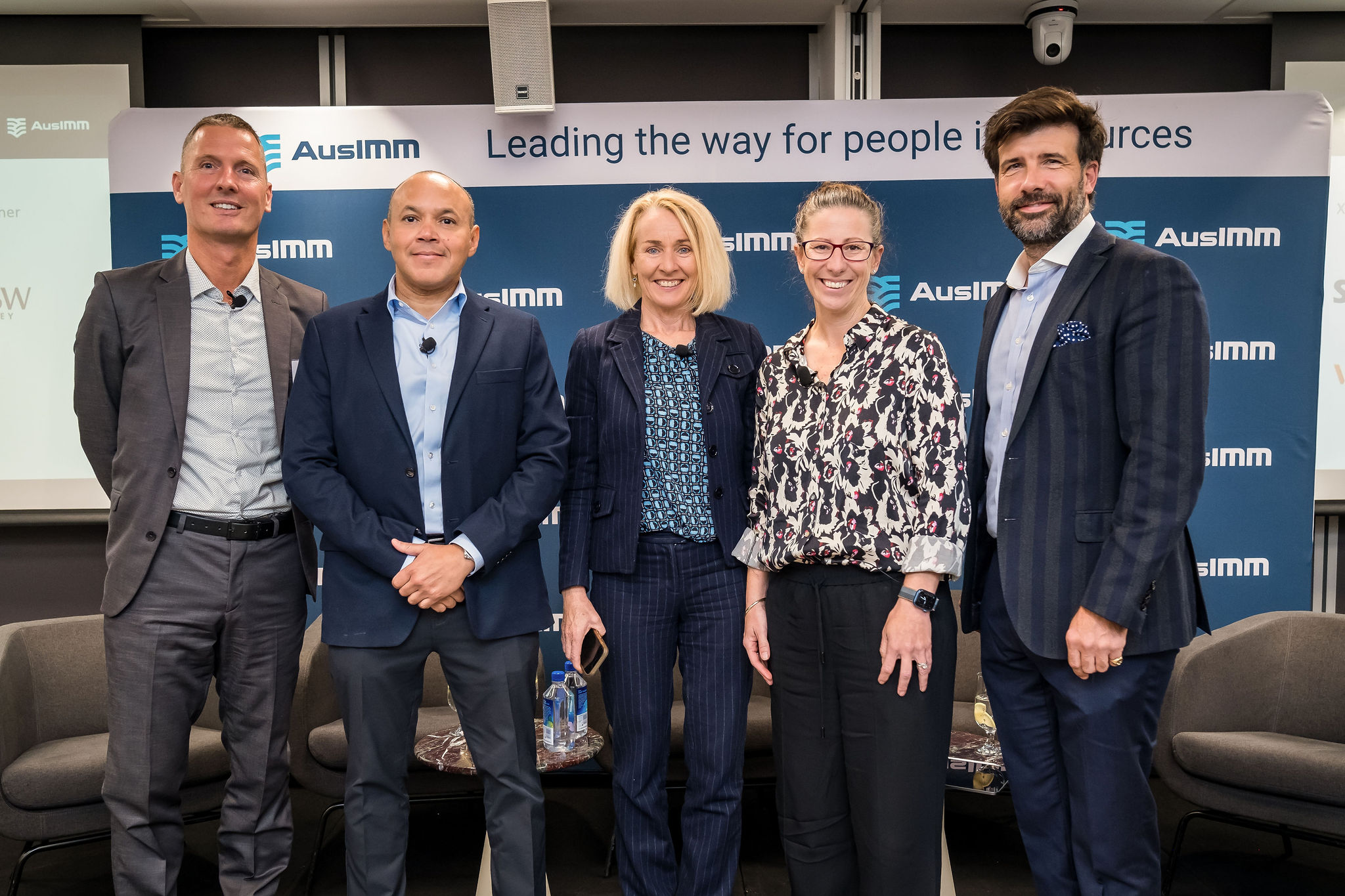
AusIMM's 2024 Thought Leadership Series launched in Perth, Western Australia, featuring its first panel discussion titled 'Innovating for success in a digital era'. This article explores key insights from the live event, now accessible for online viewing. Register for free to access the exclusive recording.
Integrating new technologies is a key challenge in front of miners. However, merging the best new and established thinking is the industry’s real test, according to leaders on an AusIMM panel.
“Success is actually when we get the balance between invention and adoption right,” idoba CEO Sarah Coleman told a large gathering at the first 2024 AusIMM Thought Leadership Series event in Perth, Western Australia.
“If we don’t put enough emphasis on the adoption and don’t put people at the centre of that adoption we run the risk of developing technology [that] people aren’t using.”
Former senior executive at GE, Brown & Root and Woodside Petroleum, Mary Hackett, was more blunt: “If your workforce don’t like what your introducing you’re dead in the water.
“All technology will fail if you’re workforce aren’t onboard.”
The forum focusing on digital-era innovation and adoption in mining heard about early automation and digitalisation successes that were encouraging more mining company boards to investigate the use of these and other technologies.
Electrification studies were starting to point to faster, feasible paths to incremental fleet change essential to companies being able to meet decarbonisation goals.
AI loomed larger as a game-changer.
The technologies are often presented as potentially threatening to people and their jobs, making change management more difficult, if not impractical.
Overall autonomous truck and drill adoption in mining remains at low, single-digit percentage levels even though workforce safety is demonstrably improved and utilisation of expensive capital equipment continues to edge higher on the back of better connectivity and fleet management.
It’s not the no-brainer it could be.
“We see lot of business cases [for autonomy] built around that 7% improvement in utilisation,” said Marcel Stoelman, Epiroc’s autonomous haulage system project director and former Caterpillar regional technology manager in Australia.
“But where I’ve seen amazing things happening [is where] people let go of their traditional way of doing things and stop adapting automation to their existing processes.
“[This] gives you what you do today, just in a more consistent way.
“Automation is not a magic bullet.
“But once I start optimising my processes to suit automation that is where we see amazing things happening.
“I have seen 20% improvement [in utilisation] at one of the mines we’ve worked at.”
Coleman, whose fast-growing technology and consulting start-up is part of one of the world’s largest contract mining and drilling companies, suggested mining was sitting on a threshold that could precede significant positive change if it could adapt fast enough to the mega shifts in technology and work reshaping most industries.
“We do have autonomous trucks in our industry but my argument is that we have remote control trucks because we haven’t actually done the work to pivot and say, how do we pull all this together.
“We’ve still got a manned operation that we’ve put autonomous trucks in and we’re still running it the same way.
“More than ever as we start to move into the world of electrification we have to start thinking of this as a system.
“We now know electrification is feasible. The numbers are stacking up. But it does require a shift in thinking and how we think about how systems go together.
“We get the technology to a certain point but it is the people and behavioural bit that’s often missing, that would enable us to get to true optimisation of the system.”
The forum heard miners were shifting on diversity of boards and workforces but were not yet equipped for more diverse thinking. That started at the top.
“If we’re trying to solve some of these problems around ESG and the complexity that comes with that, if we think the same thinking that got us to where we are today is going to solve that then we’re probably not going to solve it at the speed, or at the creative level, that we can if we embrace different thinking,” Coleman said.
“When we started idoba we acquired another three organisations. One of the teams we acquired is 90% neurodivergent. We had a team that was highly extroverted. We’ve got mining engineers.
“Managing multi-diversity teams and getting that true diversity of thought is actually really challenging.
“While it sounds nice on paper … it actually requires a huge amount of challenging your own biases and thinking differently.
“You can’t say that the onus is on the [diverse] person to think differently, you actually have to think differently as well. I know that my leadership has evolved a lot through that.
“It is amazing when you get the breakthrough ideas that can happen.
“But if we keep doing things the same way in mining, with the same thinking and the same people, we’re not going to get a different result.
“I keep saying, everyone wants to transform but no-one wants to change.
“We talk a lot more now about fast failure and that we’re open to failure, but that’s not necessarily true.
“We need impetus to create an environment that [says] it’s okay.
......................................
To continue reading the full article, click here.
AusIMM acknowledge Invest Mets for their publication of the original article.